By Ashley Gee
Built in America’s wettest city, this new aircraft factory required extensive, innovative waterproofing to ensure the foundation and tunnels stayed dry.
Contrary to popular belief, Seattle is not the soggiest city in the United States. That honor goes to Mobile, Alabama with 67 inches of annual rainfall. So when Airbus—the massive European aeronautics company— decided to build its first U.S. manufacturing facility near Mobile Bay, it created an ironic set of circumstances for the contractors: how to contend with the problems of excessive ground water when building a factory designed to put jetliners in the air.
The Airbus plant employs 300 local workers to build A319, A320 and A321 model jetliners. When construction got underway, it proved challenging to find the right waterproofing solutions. Waterproofing specialist Ram Construction Services and the general contracting firm of Brasfield & Gorrie worked with Service Construction Supply to locate suitable waterproofing and moisture control products. The distributor pointed the contractors towards W.R. Meadows products.
A Mile Long Tunnel
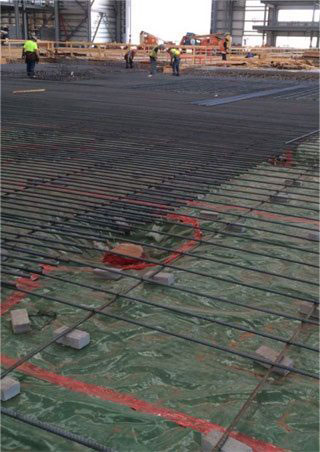
A puncture-resistant underslab vapor barrier was installed prior to pouring the floor of the main assembly building.
Jeremy Dunaway, Ram Construction’s regional manager, says, “There were significant challenges related to groundwater every time it rained.” One major concern was waterproofing a series of tunnels stretching a mile long, 15 feet below the main production floor where commercial jet liners would be assembled.
“Despite working under a roof, the groundwater we had to contend with was substantial,” said Dunaway. “The facility sits very close to Mobile Bay, so every time we had rain, the water table would rise significantly.”
Even small amounts of precipitation required pumping out the tunnels under construction and laboriously drying them before waterproofing work could resume.
The tunnels are used for utility piping, and to provide a safe walking area around and the 700,000-sq.-ft. building.
For this main assembly building, the general contractor began by laying out a puncture resistant underslab barrier called Perminator. It’s ideal for heavy traffic construction areas. With the mud slab in place, work began on waterproofing the floor of the tunnels, which was applied blindside.
Detailing was a challenge. Dunaway says, “There were hundreds and hundreds of piles driven in to support the tunnel floors. Before the concrete trucks would arrive, we needed to first treat around those pilings and then lay down the [blindside membrane] and then roll it out onto the edge forms for the tunnel foundations.”
To relieve hydrostatic pressure buildup, the Ram team also installed Mel-Drain, a dimple-drain sheet bonded to a geotextile to allow the passage of moisture through the fabric while preventing fine soils from entering the drainage channel.
“After the concrete was poured on the slab and the walls went up,” continued Dunaway, “we treated the walls. We just kind of paced ourselves all the way down the tunnel.”
In the five months it took to complete the job, Ram used 40,000 sq. ft. of Precon blindside membrane and 65,000 sq. ft. of wall waterproofing.
Moving Upward
General contractor Brasfield & Gorrie is based in Birmingham, Alabama. Keith Underwood was superintendent of their 65-man crew. “We spent nearly two years working on that job,” recalled Underwood. “We did the foundation piling, then the foundation and when that was done, we worked on the build out.” Like the Ram crew, Underwood’s team employed pumps “pretty much 24/7 to keep things dry so we could work.”
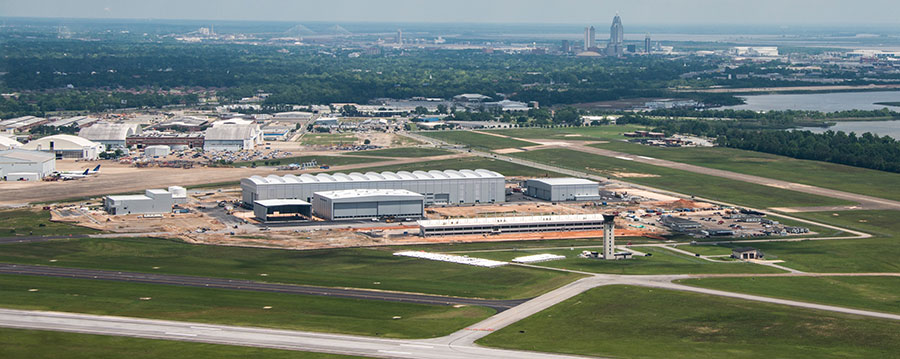
The massive plant has capacity to build up to 50 jetliners a year. It opened for operation in September 2015.
Local Distributor Was Key
A common denominator for both contracting firms was Service Construction Supply, conveniently located across the road from the Airbus construction site in Mobile.
“Gil Roberts [president of Service Construction Supply] and his company played an integral role for us on the Airbus project,” said Ram’s Jeremy Dunaway. “We were not allowed to store material in bulk on the site, and through a pretty good working relationship with them (Service Construction Supply), they were able to provide us with a steady stream of the materials we needed. They really helped us in other ways, too.”
“I knew the general contractor Ram was working with,” said Roberts, “so I was able to feed back information to Jeremy about scheduling and other job issues that were going to cause problems. It helped Ram get off to a good start. The concrete pours were coming in so fast that we had to make sure Ram was getting the materials needed to keep up with the fast-paced scheduling.”
Another important key to the successful operation was W.R. Meadows’s sales manager Michael Cripps. From the initial planning, Cripps worked with Ram engineers in Michigan on specifying the right waterproofing products for the job. And once the job began, sales personnel made periodic site visits to ensure work went smoothly.
The massive assembly building gives Airbus the capacity to build and rollout up to 50 jetliners a year. It opened for operation in September 2015.
Ashley Gee is marketing com-munications coordinator at W. R. Meadows, Inc. She can be reached at the company website www.wrmeadows.com.
Winter 2019 Back Issue
$4.95
Trade Show Preview
Drying Out a Waterfront Crawlspace
Waterproofing Industry Forecast
Securing the Roof Membrane Perimeter
Carbon Fiber for Structural Repair
Waterproofing an Airplane Factory
AVAILABLE AS PDF DOWNLOAD ONLY
Description
Description
Additional Info
Additional information
Magazine Format | Digital Download Magazine, Print Mailed Magazine |
---|