Low-voltage testing is especially useful on green roofs, such as this Chicago City Hall installation, because overburden can stay in place and the roof doesn’t have to be perfectly dry.
Leaky roofs cost American businesses billions of dollars annually, with damage ranging from minor water stains and electrical outages to complete structural failure of the roof.
Fortunately, new leak detection methods have been developed that can locate even the smallest defects with pinpoint accuracy, in either new or existing roofing and waterproofing assemblies. Electronic leak detection (ELD) identifies breaches in the roof membrane by monitoring electric fields set up above and below the membrane surface. Peter Brooks, principal at Vector Mapping/IR Analyzers, says, “Unlike the interpretive process of flood, infrared, or nuclear testing, ELD detects membrane faults directly. Even pinhole leaks invisible to the naked eye can be identified, and repairs can be made on the spot and immediately retested to ensure watertight results.”
History
For much of the 20th Century, flood testing was the preferred method of finding leaks. It’s still used occasionally, but it’s time-consuming, messy, and in some cases, the sheer weight of the water can actually damage the roof. Because of these shortcomings, various other methods were developed in the 1960s and ‘70s, including infrared thermography, nuclear moisture testing, and electrical impedance testing. These technologies are less invasive and more reliable than flood testing, but they still suffer from several significant drawbacks.
Primarily, all these “leak detection” methods actually test for moisture. None of them can detect a leak until water has built up in the insulation and other absorbent parts of the roof. The damage at that point is usually extensive. Second, because they test only for moisture, they don’t reveal the actual location of the leak. That work must be done separately—often on hands and knees.
Modern Methods
Europeans began experimenting with electronic leak detection in the 1980s, and by the mid-1990s, had developed two methods that were far superior to existing technologies.
Brooks says, “ELD is a faster, safer, more accurate and less expensive way to find leaks in low-slope roofing and waterproofing membranes. It goes by different names, but it all stems from the same basic breakthrough: using electrical current to precisely locate membrane breaches.” (Even the high-voltage method generates only a very small amount of current to minimize electrical hazards.)
During the testing, technicians create an electrical field on the membrane surface and a second electrical field in the structural roof deck (or other conductive material beneath the membrane). If there is a breach, the electric field above the membrane completes a circuit with the field below the membrane, triggering the testing device. The technician then pinpoints the location of the breach using sophisticated handheld equipment.
Low-Voltage
The low-voltage testing method was developed in Europe in the early 1990s. Technically described as “low-voltage impedance testing” it’s called Electric Field Vector Mapping (EFVM) by International Leak Detection, the company that imported the technology to North America.
Chris Eichhorn, owner of International Leak Detection, explains, “EFVM was developed by an electrical engineer in Germany, and although the principle worked, he had a hard time explaining the system to those that might be interested.” Eichhorn founded International Leak Detection in 2001 to commercialize the technology.
Low-voltage ELD involves laying a conductive wire loop around the area to be tested, wetting the membrane, and running low-voltage current through it to create an upper electrical “plate”. On ballasted and green roofs, the overburden often contains enough moisture that additional wetting isn’t necessary. A second lead is connected to the structural deck, which acts as the lower electrical plate. The membrane in between the two plates acts as the insulator.
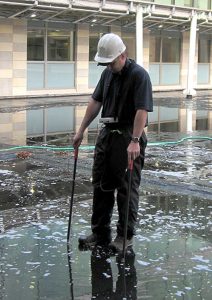
Low-voltage testing requires a wetted membrane.
Water is an extremely efficient conductor, and any defect, hole, or open seam in the membrane will allow an electrical connection between the two plates. The technician, using specialized probes, can determine which direction the current is flowing, thereby determining the location of the defect. By taking additional readings, the technician can pinpoint the exact locations that need to be repaired.
Note that in order to prevent false-positive readings, grounded penetrations within the test area must be isolated using wire loops that are connected to the perimeter trace wire. When multiple breaches are present, each individual fault must be either repaired immediately or isolated from the test bed with a temporary wire loop connected to the perimeter trace wire.
Low-voltage ELD is Europe’s most widely-used method for detecting roof leaks, and is rapidly being adopted by manufacturers, contractors, and specifiers in the United States. It’s proven to be so effective that many major membrane manufacturers now accept or even require ELD before issuing a warranty for newly installed materials. For example, Sika Sarnafil, Carlisle Construction Materials and Kemper all incorporate International Leak Detection’s EVFM testing as part of their long-term roof warranty programs.
High Voltage
High-voltage electrical testing also has its roots in Europe, and evolved out of a technique used to test coatings on metal pipes.
This method requires the membrane to be dry and exposed. One lead from the portable “pulse generator” is connected to the structural deck, and the other is attached to device resembling a push broom with copper bristles. As the operator “sweeps” the surface of the membrane, any breach in the membrane will complete the circuit between the measuring device and the roof deck. Although the testing is often conducted at relatively high voltages, the amperages are extremely low—similar to static electricity.
Limitations
Both ELD methods are extremely versatile, but there are limitations.
For instance, they require conductive roof decks. Metal and concrete—the two most common materials in commercial roof decks—work well. Wooden substrates and traditional roofing systems (with the insulation layer placed between the membrane and the roof deck) are typically not testable. To get around this limitation, alternative grounding media can be installed below the waterproofing membrane during construction. ILD developed a conductive medium about ten years ago, which makes it possible to verify the integrity of newly installed membrane that would have previously been unsuitable for EFVM testing. This medium comes in a variety of materials, such as a conductive glass felt, aluminum mesh or a highly conductive stainless steel grid.
This “detection membrane” can also be used to check for leaks on a regular schedule. Similarly, on ballasted and green roofs, a trace wire for low-voltage ELD scans is sometimes installed during construction between the membrane and the overburden to facilitate future leak detection scans.
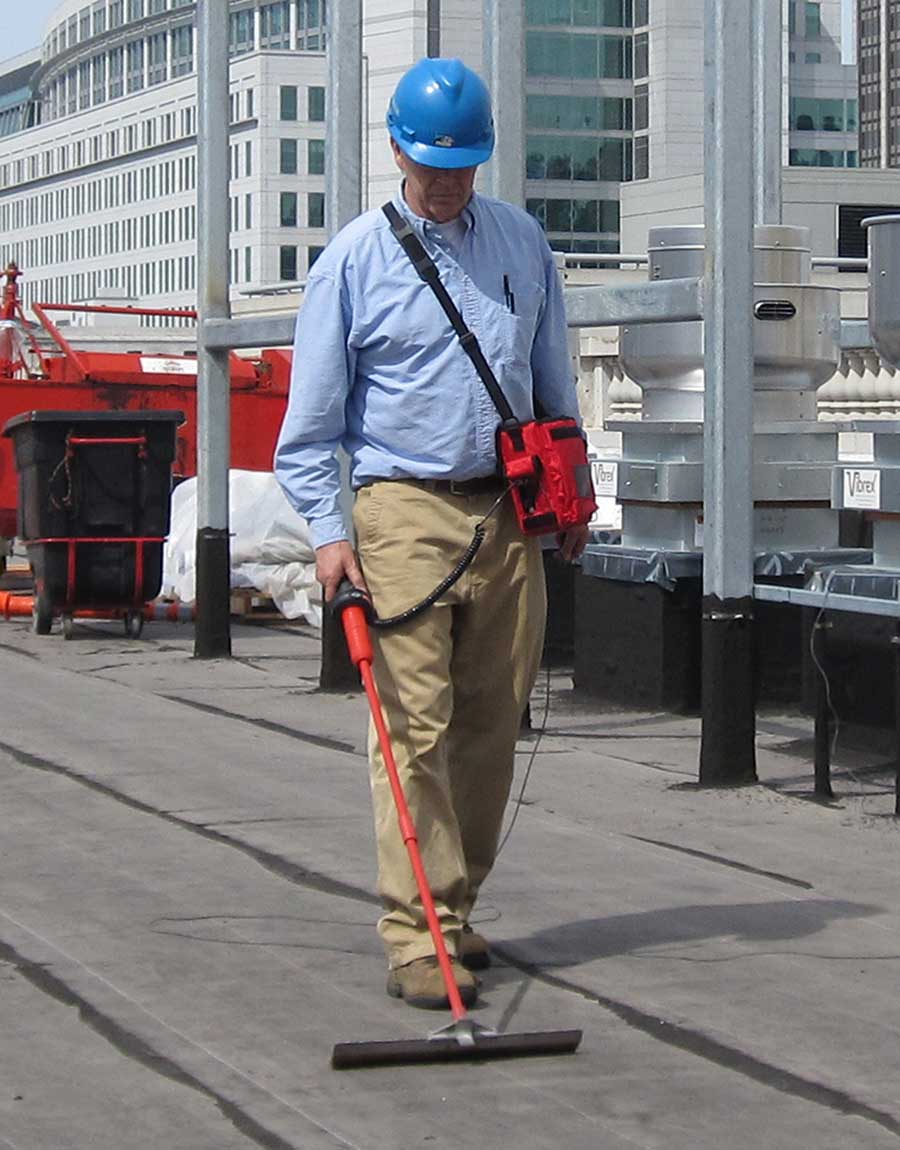
High-voltage testing requires a dry, exposed membrane.
Finally, while ELD works with a wide variety of membrane types—as nearly all roof membranes are non-conductive—there is one notable exception. Black EPDM, a popular rubber single-ply, contains significant amounts of carbon black which makes it electrically conductive. ELD testing will not work on black EPDM roofs, but is suitable for factory-laminated white grey, tan, and other lighter color EPDM.
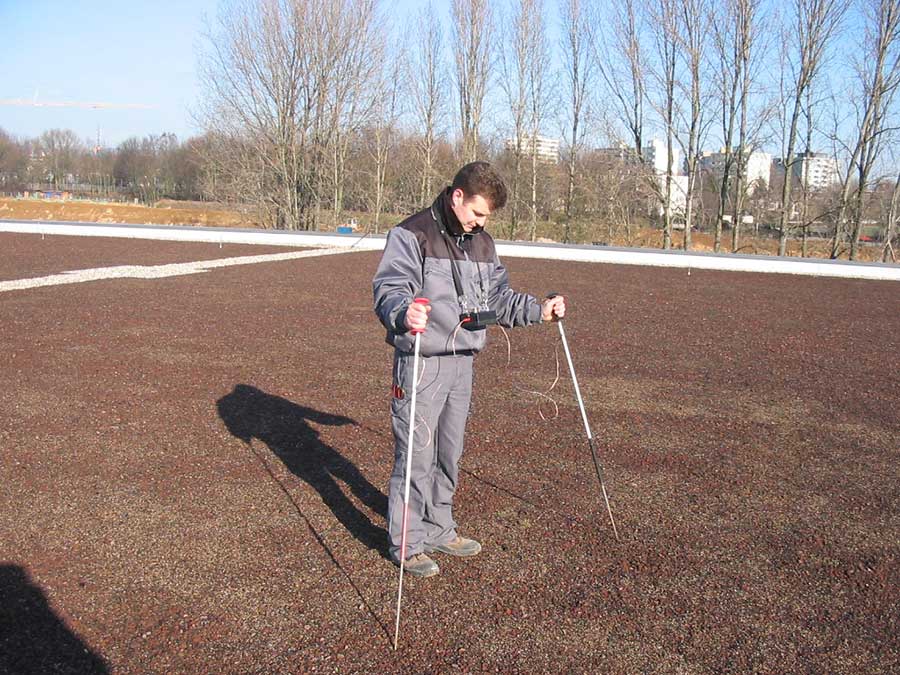
Low-voltage testing is suitable for large areas, can be employed on sloped surfaces, and allows for repairs to be made and retested immediately.
Which System Is Best
Both low-voltage and high-voltage systems have advantages and limitations. Selecting the most appropriate technology will minimize cost and deliver the most accurate testing results.
High voltage testing can be conducted by a single technician and often takes less time to complete, so it can be a more cost-effective choice.
However, it requires the tested area to be completely dry and exposed, so for roofs with overburden, such as ballasted or green roofs, low-voltage testing is nearly always a better choice, as the overburden would need to be removed for any other method. Also, high-voltage methods may not be as sensitive to defective seams as low-voltage testing.
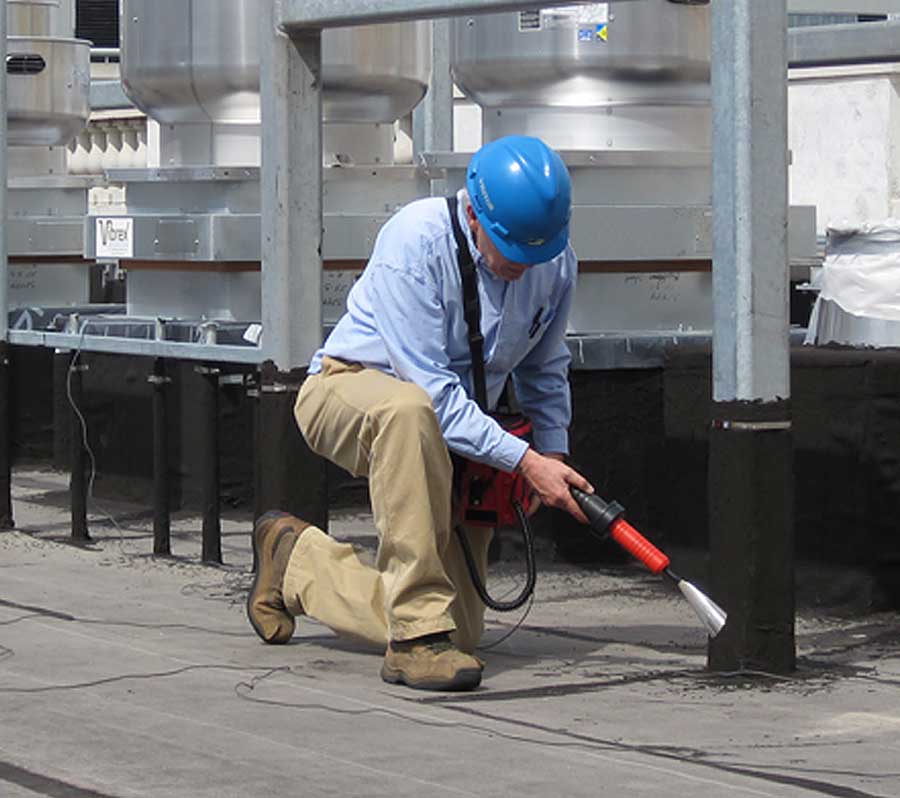
ELD can also test waterproofing on vertical surfaces, including foundations, parapet walls, and non-metallic flashings
Low-voltage ELD does require a trace wire to be set up, which takes time, but it allows for testing without having to wait for the membrane to dry—which may be an overall timesaver in damp climates.
Green Roof Considerations
Eichhorn says, “EFVM is exceptionally well-suited for green roof and ballast roof systems, because overburden can stay in place during testing, and the roof doesn’t have to be perfectly dry. It can be employed on sloped surfaces, and repairs can be made immediately and retested.”
Eichhorn does caution that root barriers can present a challenge during testing, as they prevent the tips of the probe from contacting the actual waterproofing membrane. “We can sometimes get directional flow for a general area,” he says, “but to pinpoint the exact location, you’ll need to penetrate the root barrier.”
Going Vertical
Electronic leak detection is also useful for moisture testing vertical surfaces, such as foundations, parapet walls, and non metallic flashings. While ASTM has not yet established standards for electronic leak detection, both high- and low-voltage methods have a proven track record. High voltage ELD might be preferable in hot, dry weather, as there’s no need to maintain a moist surface during testing. (In wet climates, care must be taken to ensure that all test surfaces are completely dry.)
Eichhorn notes that low-voltage EFVM is also perfectly capable of testing vertical surfaces. “EFVM is a great tool for testing walls,” he says. “We’ve been doing this type of testing since 2004 with great success, and the number of clients requesting this type of testing is steadily increasing.”
Conclusions
ELD is rapidly becoming the new leak detection standard in Europe and North America. Suitable for testing membrane integrity during construction and forensic leak detection years after installation, it has been specified on some of the nation’s most prominent roofing projects.
While high-voltage and low-voltage systems differ considerably, both save time and money, and can work with a wide variety of rooftop waterproofing assemblies. Both methods are usually far superior to older technology because they pinpoint the actual breach in the membrane, not simply the presence of water, and repairs can be made and re-tested immediately.
Fall 2013 Back Issue
$4.95
Electronic Leak Detection: High Vs. Low Voltage
Basement Finishing Kits
Blindside And Underslab Work
Project Profile: Monterey Bay Aquarium
AVAILABLE AS DIGITAL DOWNLOAD ONLY
Description
Description
Electronic Leak Detection: High Vs. Low Voltage
The need to quickly find and repair leaks in roofing membranes has never been higher. Two new electronic leak detection methods are rapidly gaining popularity because they can locate even the smallest leaks with pinpoint accuracy.
Basement Finishing Kits
By Ron Greenbaum
It’s now easier than ever to offer basement finishing services. A number of companies offer innovative prefinished “kits” that make this a profitable service for many waterproofing contractors.
Blindside And Underslab Work
Projects that require waterproofing to be installed before the structural concrete require reliable, durable products, and flawless workmanship.
Project Profile: Monterey Bay Aquarium
By Steven H. Miller
Rebuilding and sealing a million-gallon aquarium tank was challenging—especially with a tight timetable and a requirement for non-toxic materials.
Additional Info
Additional information
Magazine Format | Digital Download Magazine, Print Mailed Magazine |
---|