As building envelopes have gotten tighter, radon has become deadlier. Underslab barriers, radon mitigation, and testing systems are healthy—and profitable—services basement contractors can add to their businesses.
Radon is a cancer-causing radio-active gas. Invisible, odorless, and undetectable to the unaided human, it can cause serious health problems. In fact, the U.S. Center for Disease Control estimates that radon is the leading cause of lung cancer among non-smokers, and the second leading cause of lung cancer overall in the United States today, causing more than 21,000 deaths annually.
Present in most areas of the country, radon barriers—a variation on the underslab moisture barrier—are the first line of defense. Not only do they improve the health and general livability of the structure, but they also can provide additional income to a waterproofer’s bottom line.
“As building envelopes have gotten tighter, we’ve learned to protect the indoor environment from too much moisture. We should have the same concerns about other vapors coming into structures from the soils, passing through the slab through cracks in the concrete,” says Bryan Coulter, vice president at PolyGuard.
“Over the past 15 years, we’ve become especially aware of the need to prevent radon from entering residential structures,” he continues. “On the commercial side, schools, hospitals and other buildings with high occupancy rates are also prime candidates for radon prevention.”
The Danger
Radon is a naturally occurring element, and is quite common. It’s a byproduct produced from decomposing uranium ore and other minerals deep underground. Being lighter than the surrounding soils, the gas seeps upward through small spaces in the soil and rock to the surface.
Radon gas is, however, the heaviest gas known to exist—nine times heavier than air—so when there’s no wind to help the gas dissipate, it builds up indoors in basements and other low-lying areas. According to Michael White at HomePro Inspections.com, most radon enters a home through dirt floors, cracks in concrete, sumps, joints, basement drains, etc. “Concrete-block walls are particularly porous to radon,” he says.
Historically, buildings have been drafty enough that indoor radon levels never presented any health risks. However, as building codes have mandated tighter, more energy efficient construction, radon has become a serious issue. “Radon-related health problems have increased dramatically in recent decades,” stated U.S. Surgeon General Richard H. Carmona in 2005. “In just the past 25 years… evaluations related to air quality concerns have increased from one of every 200 evaluations to one of every two.” But it’s not because radon is becoming more common; it’s because it’s more easily trapped inside our living spaces.
The issue has become so important that Carmona issued a National Health Advisory in 2005, warning, “Radon gas in the indoor air of America’s homes poses a serious health risk [and] breathing it over prolonged periods can present a significant health risk to families all over the country.”
The issue is serious enough that every state in the U.S. has a radon information office. These experts are the best source for finding out whether elevated radon levels are common in your area.
Just as uranium decays into radium, which produces radon, this gas decays further into radioactive elements known as “radon daughters.”
“Radioactive daughters float around in the air attached to dust and to smoke particles,” explains White. “When inhaled, the particles find their way into the bronchial air passages—your lungs—and stick to the surface. When these particles decay further, they emit a tiny burst of radiation strong enough to damage cells. This increases your chance of developing lung cancer.”
Although this damage does not make people feel poorly on a day-to-day basis, the effect of radon exposure is long term. Smokers and children are particularly susceptible.
The Solution
“It’s important to know that this threat is completely preventable,” says Dr. Carmona. “Radon can be detected with a simple test and fixed through well-established venting techniques.”
For waterproofers that are already in the business of improving the livability of below-grade living space, it may be smart to add radon mitigation to the list of services the company provides.
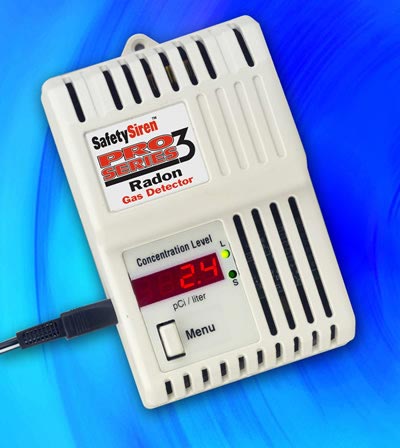
One-time radon test kits are available, but many homeowners prefer the accuracy of professional testing. Long term monitors that offer constant surveillance are also popular.
The need for this service is vast. The U.S. Environmental Protection Agency (EPA) reports elevated radon levels have been discovered in every state, and affect between one-in-five and one-in-fifteen homes. It could be as many as eight million structures throughout the country. (The EPA defines “elevated” as more than 4 picoCuries per liter (pCu/L) of air, about triple the normal background level.)
Testing: Radon testing is a good first step for the concerned homeowner. It’s also a good first step for contractors trying to get into the business. Most individuals will be happy with a one-time test to verify that radon levels in their home are not an issue. Do-it-yourself testing kits for homeowners are available for around $50. More than a quarter million are sold annually, nearly all use activated charcoal to trap radon, which is sent to a lab for analysis.
Trained professionals use equipment that is far more accurate. For much of the 1990s, the EPA ran a “National Radon Proficiency Program” that trained, tested, and certified radon detection equipment and the contractors who installed them. That program was discontinued in 1998, when they handed these duties over to a pair of private organizations, the National Environmental Health Association (NEHA) and the National Radon Safety Board (NRSB). Both are highly regarded, and have information on their websites on how to become certified.
Basement remodels, which waterproofers are often involved with, should include radon testing before work begins. If test results indicate a problem, radon-resistant techniques can be inexpensively included as part of the renovation. Because major renovations can change the level of radon in any home, test again after work is completed.
Testing is fairly straightforward. Because radon is much heavier than air, the testing device is placed in the lowest lived-in level of the home; the basement if it is frequently used, otherwise the first floor. The EPA advises, “Place the kit at least 20 inches above the floor in a location where it won’t be disturbed—away from drafts, high heat, high humidity, and exterior walls. Leave the kit in place for as long as the instructions indicate. Once you’ve finished the test, reseal the package and send it to the lab specified on the package right away for analysis.”
Monitoring: If the one-time test result is above the four pCi/L threshold, the EPA recommends a long-term monitoring system to gain a better understanding of the year-round average radon level. In high risk areas, homeowners may want a radon-monitoring system installed from the beginning, similar to smoke detectors or carbon monoxide detection system. These are available from a number of manufacturers and are usually hard-wired into the home.
Mitigation: If test results indicate more than twice the EPA’s 4 pCi/L action level, a mitigation system should be installed.
In certain high-risk areas, radon mitigation systems are required by law for all new construction. Five states require radon venting systems for all new construction; an additional 22 require it is some jurisdictions.
The National Association of Home Builders (NAHB) reports that about one home in every six is being built with a radon mitigation system. In high-risk areas, the percentage increases to one in three.
Construction Options
The most common technique is a “passive sub-slab depressurization system,” consisting of a vent pipe extending from below the floor slab to the attic. If the pipe is routed through warm space (such as an attic or furnace flue), the temperature difference will cause the radon to rise through the pipe and vent harmlessly into the atmosphere. A simple vent pipe, properly installed, reduces radon levels by about 50%. Sealing foundation cracks and other openings makes this kind of system more effective.
If the system is being installed while the home is under construction, contractors can dramatically improve the efficiency with a few simple steps. The NAHB says, “Radon-resistant new construction (RRNC) typically costs a builder between $250 and $750,” and could cost even less “if the builder already uses some of the same techniques for moisture control.”
ASTM has established minimum guidelines for radon mitigation systems under E 1465-06 Standard Practice for Radon Control Options for the Design and Construction of New Low-Rise Residential Buildings.
The technique is almost identical to underslab moisture control. Begin with a layer of clean, washed gravel. RRNC standards call for ½” or ¾” aggregate a minimum of four inches deep. In areas where gravel is cost prohibitive, perforated pipe can be substituted.
This is topped with an underslab vapor barrier. The minimum acceptable thickness is 6-mils, but for crawlspaces and other exposed areas, 8- or 10-mil would be a better choice. Cross-laminated polyethylene is even more durable. Seams between adjoining sheets are usually overlapped a minimum of 12 inches and sealed with a continuous bead of sealant. A few products have a ribbon of adhesive pre-applied. Others are dimpled and interlock. The joint between the underslab barrier and the footer must be sealed as well.
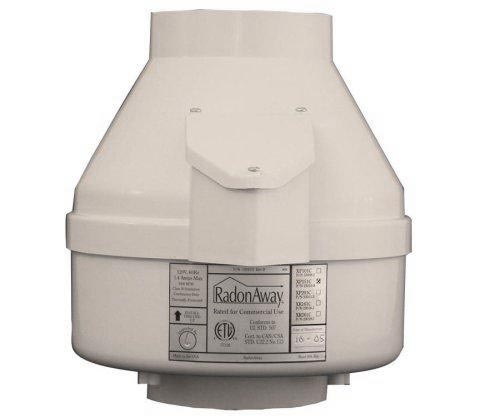
If passive ventilation isn’t enough, in-line fans like the one can be easily added to the vent pipe to lower radon levels even further.
“An effective underslab gas barrier needs to be able to withstand construction traffic and the stress of placing concrete directly on top of the barrier,” explains Tom Stoebner, Business development manager for Raven Industries, “A gas/moisture barrier will not perform as intended if it is susceptible to pinholes caused by construction traffic… It must be able to withstand rips and tears from common construction traffic such as pump hoses, reinforcing bar placement and other job site hazards.”
Stoebner argues that even though the EPA and ASTM have claimed in the past that a 6-mil polyethylene sheet is adequate, “over the years the industry has discovered that 6 mil polyethylene is not acceptable as an underslab gas barrier, let alone a moisture vapor barrier due to the susceptibility to installation damage and high permeability to gas and moisture vapor.”
He recommends ASTM E 1745-09 “Standard Specification for Plastic Water Vapor Retarders Used in Contact with Soil or Granular Fill under Concrete Slabs” as a starting point. This standard requires tensile strength of no less than 45.0 lb/in. and a puncture resistance of 2200 grams. To meet these requirements, most barriers are at least 10 mils thick and made with state-of-the-art resins to provide exceptional puncture strength.
Coulter, at Polyguard, points out that seams, penetrations, and edges are common failure points and need particular attention. “On our sheet, we have an extended edge to ensure that the barrier remains in place.” He recommends using an asphalt-based adhesive to seal the edge of the sheet to the footer. “That’s the proven method,” he says.
Once the sheet is sealed, vent pipes are installed to direct the captured radon out of the building envelope. Conventional 4” diameter ABS or PVC vent pipe is standard.
CertainTeed’s Form-A-Drain, used as a combination stay-in-place footing form and drain tile, can be easily adapted for radon mitigation using factory-standard parts. It forms a complete sub-slab perimeter loop around the inside of the foundation — a key element of a radon reduction system.
Depending on the lot configuration and moisture management system, the vent pipe can be sloped to daylight, directed to the sump, or vented directly through the roof.
If radon is directed to the sump, a second vent pipe would be needed to direct the gas through the roof and out of the building. This option also requires a sealed sump cover.
Finally, all penetrations must be carefully sealed, both in the lower portion of the home to reduce radon, and in the attic to ensure the vent draws well.
After the system is installed, the home should be tested again to make sure it is functioning properly. If radon levels are still above the recommended thresholds, a fan can be installed in the attic vent pipe, creating an “active ventilation system.” An alarm on a separate circuit—similar to sump pump installations—is sometimes installed to alert the homeowner if the fan malfunctions. Many builders are installing an electrical outlet in the attic with passive systems to make this an easy retrofit option.
Research from the EPA indicates that radon reduction systems are extremely effective; some can reduce radon by up to 99%. In one extreme case—discovered when the homeowner set off radiation alarms at his workplace—levels were reduced from 2,700 pCu/L to 4 pCu/L.
Additional Advantages
The primary advantage of a radon reduction system is that the homeowner will have lower in-home radon levels. But a secondary advantage is that the homeowner will enjoy a much lower level of humidity, especially if an underslab vapor barrier was installed.
The amount of radon present in a home is highly variable, and depends on a number of factors, including soil type, geology, foundation type, HVAC system, construction “tightness,” and others.
Similarly, the cost of reducing radon in your home depends on how your home was built and the extent of the problem. For more information, visit the online version of this story, which includes links to state radon coordinators, national certification boards, architectural details of mitigation systems, and an 84-page step-by-step guide for building radon-resistant homes.
In summary, radon-resistant construction techniques are effective in preventing radon entry when installed properly and completely. Installing them at the time of construction is easier and less expensive.
“Considering radon is a significant health risk with more people dying from radon-caused lung cancer each year than from many other highly publicized causes of death, why take a chance?” askes Stoebner. “The industry now offers highly innovative radon gas barriers that have a radon permeability rate 278 times lower than ordinary 6-mil polyethylene, with Class A puncture resistance to withstand demanding installation and job site stress.”
Raven Industries and Polyguard, manufacture underslab gas barriers with extremely low gas permeability.
These barriers can be a profitable and valuable service that basement repair and waterproofing contractors can easily add to their business.
Basic Radon-Resistant Construction
The techniques and materials used for radon venting are readily available. While the techniques may vary for different house foundations and building site, the five basic features are the same:
- Gravel: A 4-inch layer of clean, coarse gravel below the slab. This layer allows soil gases—including radon—to move freely underneath the house, where they will be extracted through the vent pipe.
- Vapor Barrier: A heavy-duty vapor retarder is placed on top of the gravel to prevent concrete from clogging the gravel layer when the slab is poured. The barrier should be tough enough to remain puncture free after the pour to prevent the soil gases from entering the house.
- Sealing and Caulking: In remediation work when an underslab barrier may not be possible, seal all the cracks, and crevices in the foundation walls and floor with gas-impervious caulk. Even in new construction, this step is sometimes necessary.
- Vent Pipe: A 3” or 4” PVC pipe, like the ones commonly used for plumbing vents, runs vertically from the gravel layer (stubbed up when the slab is poured) through the roof to safely vent radon outside above the house. This pipe—and the stub—should be labeled “Radon System” to prevent confusion with the wastewater plumbing. Run thepipe through conditioned space to maximize the chimney effect.
- Junction Box: Install an electrical outlet in the attic for use with a vent fan in case a more robust system is needed.
An 84 page booklet is available on our website that offers a more complete overview of how to construct radon mitigation systems—including how to seal and vent crawlspaces. http://www.epa.gov/radon/pdfs/buildradonout.pdf
Fall 2010 Back Issue
$4.95
Underslab Radon Barriers
Working With Carbon Fiber
Roof Pitch and System Selection
AVAILABLE AS DIGITAL DOWNLOAD ONLY
Description
Description
Underslab Radon Barriers
In some areas of the country, radon barriers—a variation on the underslab moisture barrier—are a great way to improve the livability of the building and add additional income to the company’s bottom line.
Working With Carbon Fiber
Stronger and less bulky than steel, carbon fiber is making basement structural repair easier than ever before. Whether its carbon straps, staples, or sheets, we explain what the options are, and how to make sure they’ll perform.
Roof Pitch and System Selection
Flat roofs obviously require different treatment than steep ones. We’ll look at the role roof pitch plays in determining how a rooftop waterproofing membrane will perform.
Additional Info
Additional information
Magazine Format | Digital Download Magazine, Print Mailed Magazine |
---|