Available in a range of profiles and materials, waterstops can play a major role in preventing water leakage in concrete joints.
In addition to membranes, coatings, and drainage, large commercial structures usually require some type of waterstop to keep groundwater from seeping into the building through joints and seams in the concrete.
These are available in a wide variety of shapes, sizes, and materials in order to meet the requirements of the different types of joints, amount of expected movement, hydrostatic pressure and chemical exposure.
Selecting a Waterstop
For non-moving joints, such as the cold joint between a footing and foundation, expanding waterstops may be a good choice. Many products in this category use bentonite clay as the active component, but others use some other compound that is more forgiving of saltwater, chemicals, repeated wet/dry cycles and so on.
Regardless of the precise form-ulation, these products work on a similar principle: Exposure to water makes the material expand dramatically, enough to create a compression seal and stop water from penetrating the joint.
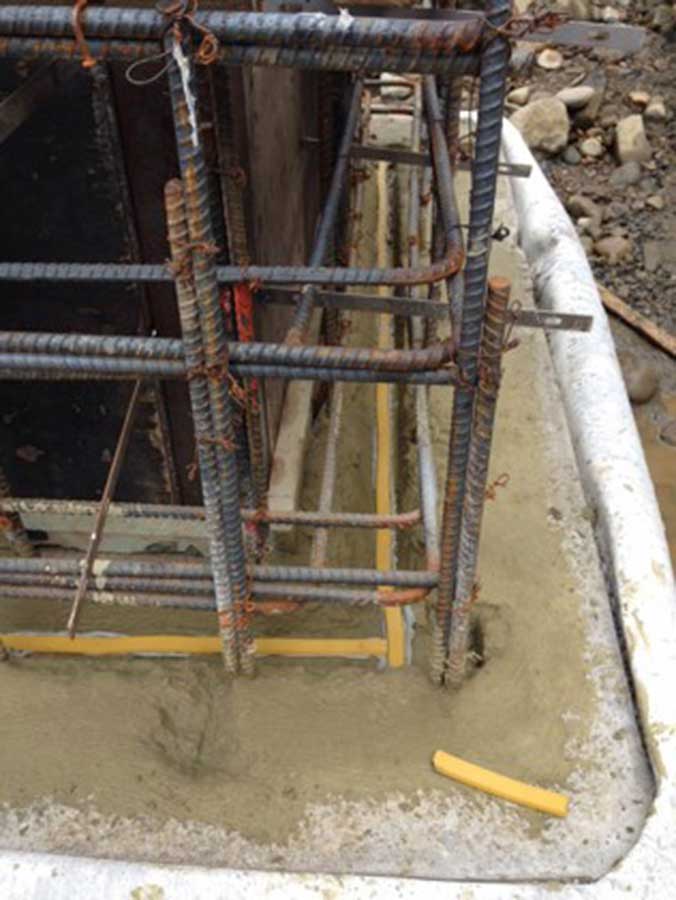
The waterstop image at right shows the robust joint detail, including treatment slurry and expandable waterstop (in yellow). The grout infill will be placed in the space blocked out by the blue rigid foam insulation.
Application is usually a matter of fastening the strip in or along the joint. Again, because this seal is easily broken, hydrophilic waterstops are suitable for non-moving joints only.
Crystalline products are also sometimes used to waterproof non-moving cold joints. Moving joints require mechanical waterstops, the type that spans both sides of the joint to create a diaphragm. Neoprene, PVC, and rubber are commonly used materials. These are ribbed, or have a thicker “dumbbell” of material on the ends to keep them in place and ensure maximum water-sealing performance. Profiles with a “bubble” in the middle of the strip are best for joints with lots of movement. In new construction, one side of the stop is embedded in the concrete during the first pour. The other half of the waterstop is encased in concrete when the other side of the joint is poured. Obviously, keeping the waterstop in place, with no folding or movement, requires considerable attention to detail. Usually it is fastened to the vertical rebar or form ties to keep it in place.
In the past decade, waterstops with integral injectable grout hoses have been developed, which allow joints to be sealed if leaks develop after construction is completed.
Regardless of the type installed, workers must ensure good consolidation around the waterstop. Those placed horizontally in slabs require particular attention, as it’s difficult to get concrete to flow into the gap between the bottom of the stop and the top of the forming bed.
T-shaped waterstops are available as a retrofit option. The flat side of the waterstop is secured to the existing concrete using epoxy or other specified adhesive, after which the new concrete is placed.
Case Study
Waterstops were part of the solution used to ensure a church foundation in the New York City Area stays dry. The evangelical church Letting Christ Be Known in the Bronx was designed with a deep foundation, and is sited on a low-lying lot very close to Long Island Sound. The ground was so saturated that when construction began, the dewatering system was removing 40,000 gallons of water per day.
New England Dry Concrete was selected as the waterproofing contractor, and installed a multi-component system of waterstops and crystalline waterproofing to seal the brackish from penetrating the structure.
Gregory Maugeri, Dry Concrete’s co-founder, says there are several versions of Kryton’s waterstop system, and the church required the most robust configuration. The Krytonite Waterstop is designed to withstand 164 feet of columnar head pressure, or about 71 psi.
He explains, “When you have water projected to be six feet up the walls, this waterstop detail is a life saver. There are very few reliable assemblies that can be used for this purpose, especially in brackish, saltwater, and chemical environments where traditional bentonite materials are not recommended.”
The first step was to treat all the cold joints with Krystol Waterstop Treatment Slurry, used to promote crystalline growth between sequential concrete pours, like walls-on-footing or slab-to-wall for instance.
Then crews glued down a non-bentonite swelling waterstop in a location not too close to rebar and with sufficient concrete cover. With all the concrete placed, crews then went back and sealed the inside face of the joints with a waterproof grout, completing the system.
The below-grade portion of the 9,000-sq.ft. church was completed in 2017, and the foundation has remained dry in the years since.
Spring 2020 Back Issue
$4.95
Options for Structural Repair
Joints and Waterstops
Electronic Leak Detection
Case Study: Shoshone Power Plant
AVAILABLE AS DIGITAL DOWNLOAD ONLY
Description
Description
Options for Structural Repair
Residential foundation repair is an urgent, growing, and profitable opportunity for waterproofers. Solutions can include piering, grouting, crack injection, and carbon fiber.
Joints and Waterstops
Available in a variety of profiles and materials, waterstops can play a major role in preventing water leakage at cold joints and expansion joints in concrete.
Electronic Leak Detection
New electronic leak detection methods can locate even the smallest leaks with pinpoint accuracy. Some systems can even monitor for leaks continuously with real-time alerts.
Case Study: Shoshone Power Plant
When a century-old hydroelectric plant deep in a Wyoming canyon was re-roofed, it included technology to ensure electronic leak detection even through the EPDM membrane.
Additional Info
Additional information
Magazine Format | Digital Download Magazine, Print Mailed Magazine |
---|