A successful waterproofing system is more than membranes. By approaching waterproofing as a system, it’s possible to identify the root cause of the problem, and the most
cost-effective solution to it.
While the word “waterproofing” typically refers to a spray-applied coating or peel-and-stick membrane, contractors who make their living by keeping basements dry understand that a successful waterproofing system is more than membranes.
It starts at the roofline with the eaves, gutters, and downspouts, and extends to landscaping, sprinklers, and ground slope. The below grade components—membranes, drain tiles, sump pumps, etc—must be specified to complement the products installed above-grade.
Whether the job is a commercial roof or a residential basement, the key to keeping water out isn’t going to be found in a single product. It’s a combination of waterproofing, drainage, and landscaping systems that must work together.
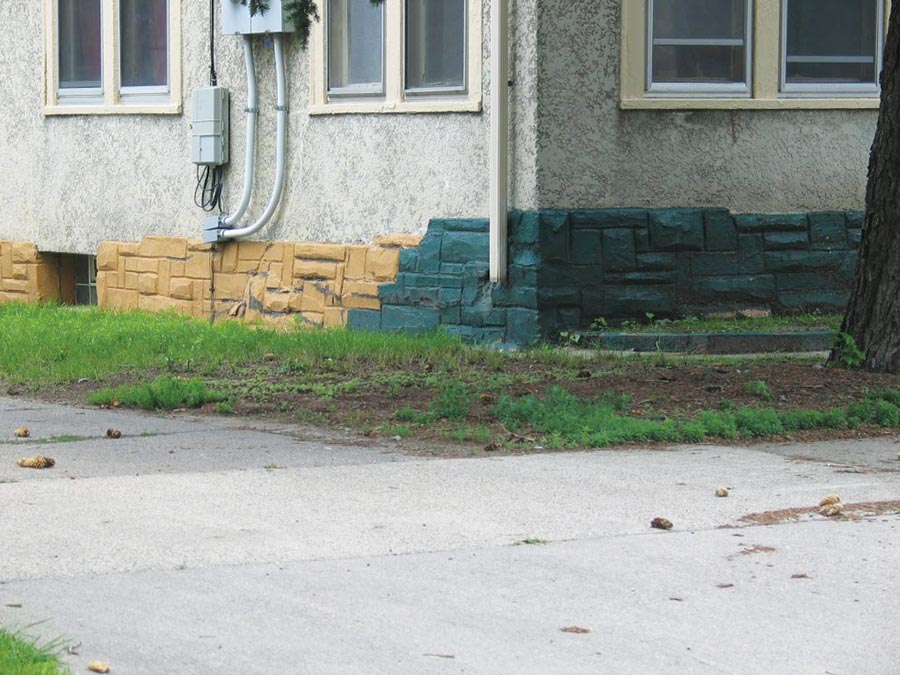
This downspout directs hundreds of gallons of rainwater directly against the foundation. Remedial waterproofers should find and remedy problems such as this before tackling more expensive areas.
Further, this system has to be designed to take into consideration the building’s climate, size, and the construction materials used. Only by treating waterproofing as a system can a cost-effective solution be found.
By approaching waterproofing as a system, it’s possible to identify the root cause of the problem, and the most cost-effective solution to it. For example, in one residential application, the solution to an overworked sump pump was found in re-sloping the flowerbeds adjacent to the home.
This approach works equally well for new construction and remediating older homes.
Start at the Top
In evaluating a waterproofing system, residential or commercial, the best place to start is where the water does: on the roof. Are gutters and downspouts in place? Do the downspouts drain near the foundation, or are they connected to extensions that deposit the water well away from the home?
During a typical rain shower, gutters can collect an astonishing amount of water in just a few minutes. (One inch of rain on a 2,000 sq. ft. roof translates to 1,250 gallons of water!) If the rainwater or water from melting snow does not get channeled far enough away from your home, it will saturate the soils near the foundation and it can eventually get into the crawlspace or basement. The wet soil may weigh enough to actually crack basement walls. This force is called hydrostatic pressure. To prevent the water from collecting near the foundation or footing, downspouts should be directed onto a non-pervious surface that slopes away from the home or connected to a set of drainage pipes.
At Grade
The solution to most remedial waterproofing is on the ground, not below it. Nearly all residential waterproofing problems can be solved by addressing the soil type and slope around the foundation. (Exceptions are situations such as a home built on top of an underground spring or in an area with a water table closer than 10 feet to the surface).
Experts agree that controlling surface drainage is the single most important factor in keeping basements dry.
The ground around the home should slope downward (away from the structure) for a distance of at least six feet. It doesn’t have to be much; two inches over the six feet is sufficient to channel water way from the foundation.
Examine the landscaping, planned or in place. Do sprinklers soak the ground near the foundation? Do leaky hose bibs saturate the soil beneath them?
Hillsides
In the past decade or so, homes have increasingly been built on hillsides or other marginal land that was passed over by developers years ago. Homes built on hillside lots are often problematic for waterproofers, as they’re sometimes in the path of all the water collected on an entire hillside.
If the water can’t be directed around the structure, a second line of defense is sometimes needed. This consists of a drain tile —a perforated pipe set in gravel a few feet below the surface or equivalent—set perpendicular to the slope of the hill a dozen feet or so uphill of the home. Water traveling down the slope will fall into the drain and be directed away before ever reaching the waterproofing barrier.
Protective Barriers
Virtually all areas of the country now require a waterproof barrier to be installed on concrete basements. The level of protection required varies, based on the expected precipitation and soil type in your area. However, millions of homes across the country were built when codes required only damp-proofing, or required nothing at all. In many cases, these asphalt-based coatings were literally brushed on with an old broom, and after years of wear have degraded to the point that they no longer function.
If all of the above-grade components check out, and the basement is still damp, any solution will likely involve applying a new waterproofing barrier. These can be spray-applied, a peel-and-stick membrane, or even a slurry coat troweled onto the wall. In every case, they work by preventing water from penetrating the foundation walls.
For new construction, integral waterproofing admixtures may be worth investigating. These work by making the concrete itself waterproof. Integral waterproofing slurry coats are also available for remedial work.
The choice of waterproofing products usually comes down to cost, effectiveness, and the homeowner’s level of confidence in the applicator.
Drainage
Regardless of the type of waterproofing applied, it’s usually covered with a drainage system of some sort. The most basic option is washed gravel. Many opt for a rigid or semi-rigid insulating drainage board; they’re light weight, protect the waterproofing membrane during backfilling operations, and insulate the below grade living space.
Sheet drains, or dimple membranes, are another option. Made by at least half a dozen companies, they’re available in a wide range of sizes, compressive strengths, flow rates, and filtration capabilities. A few dimple membrane manufacturers claim that their product can fill the roles of both a waterproofing and drainage component.
At the base of the foundation, a footing drain must be installed to move the water away from the structure. In the past, the solution has consisted of a perforated PVC pipe, buried in washed gravel and covered with straw to prevent soil from clogging the system. This system works, and is still used frequently. Prefabricated footing drains also work well. A few manufacturers offer their dimpled sheet drain and drainage tile in a single product to make installation easier.
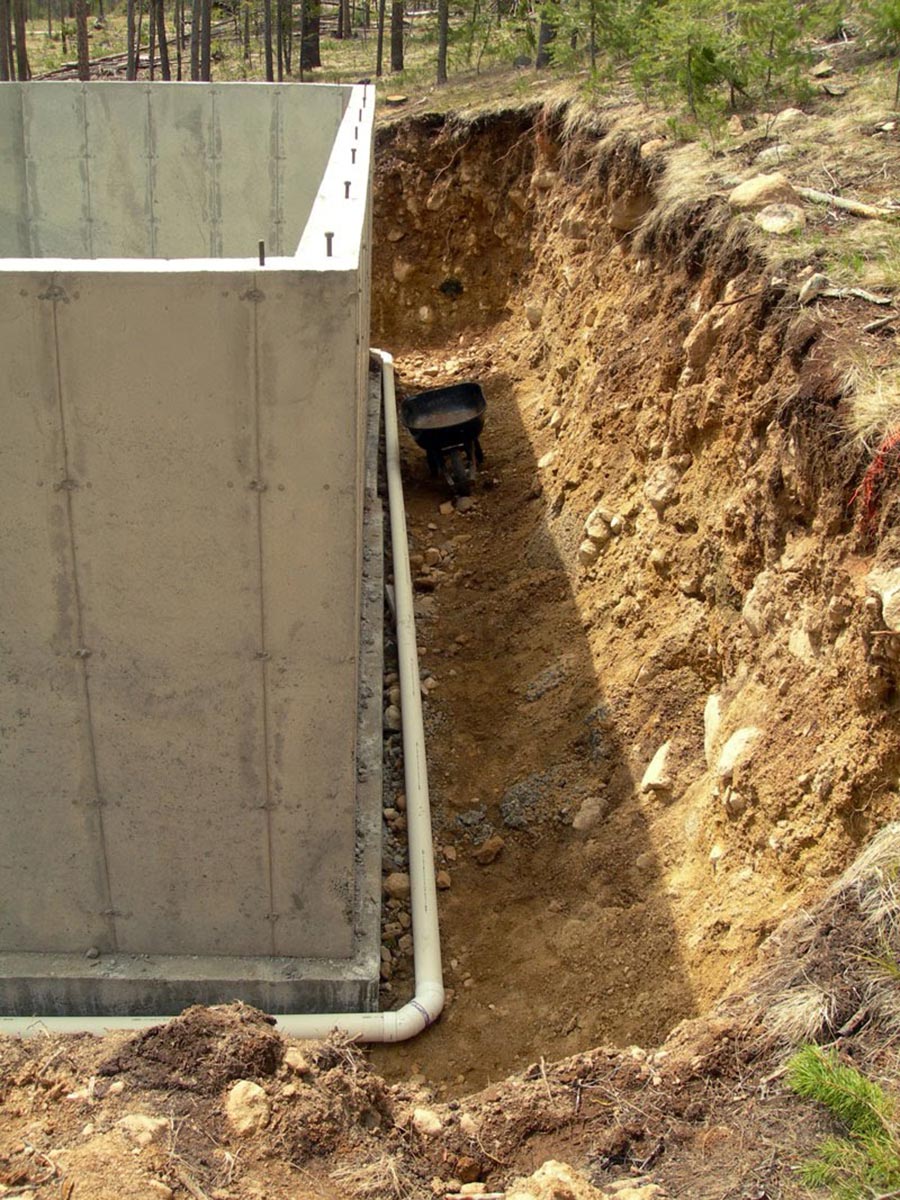
A complete below-grade waterproofing system should incorporate an impermeable membrane (top left) a drain mat (bottom left) and a footing drain, (below) all protected with pervious, non-compacting fill.
Underslab Protection
Effective control of water from the roofline to the footer will resolve nearly all moisture issues. In a few cases, though, the source of moisture issues may be coming from beneath the structure. These isolated instances can only be resolved through the use of an underslab barrier. Mostly used in new commercial construction, these heavy-duty sheets prevent moisture from migrating through the floor slab into the building’s living space.
Disposal
Once water has collected at the footings, it needs to be directed away from the structure. In most cases, this means installing or repairing the sump pump, which moves the water to either to a French drain placed well away from the house or into a storm water drainage system.
The sump pit should be sized to your climate. It needs to be large enough that the sump pump doesn’t need to run constantly to keep it empty, but not so large that it takes an inordinate amount of space.
The size, type and power source for sump pumps will depend on the application. Some are hard-wired directly into the home’s electrical system. Others offer battery back-up, or audible alarms when the water gets too high. A few can even be programmed to dial your cell phone if something goes wrong.
One final area to check for problems is the French drain, or dry well. Decades ago, these were made from 50-gallon metal barrels with holes punched in them. Over the years, they may have rusted and collapsed. If so, they’re easily replaced with plastic drywells available from a variety of manufacturers.
Winter 2012 Back Issue
$4.95
Piering for Foundation Repair
Cut-and-Cover Tunnels
A Systems-Based Approach to Waterproofing
AVAILABLE AS DIGITAL DOWNLOAD ONLY
Description
Description
Piering for Foundation Repair
Structural repair work dovetails nicely with many waterproofing businesses. With new piering methods, residential foundation repair is easier—and more profitable—that ever before.
Cut-and-Cover Tunnels
One of the most popular and cost-effective tunnel systems, this technique is popular for building subways, utility corridors, and other shallow tunnels. Here’s how they’re waterproofed.
A Systems-Based Approach to Waterproofing
A successful waterproofing system is more than membranes. It’s a combination of waterproofing, drainage, pumps—even landscaping and rain gutters—that must work together as a system.
Additional Info
Additional information
Magazine Format | Digital Download Magazine, Print Mailed Magazine |
---|