By Vanessa Salvia
The 21,600 square foot garden roof assembly at 1225 Connecticut Ave. in Washington, DC, is an example of a ballasted roof.
A ballasted roof is an assembly in which a membrane is loose laid, and then something holds it down. There’s no fastener in between the layers. Ballast is a word that typically is used in the fields of shipping, boating, or air travel to mean material that improves stability. In this usage, ballast means it is anchoring the membrane and insulation — even though there’s no adhesive, these roofs can be designed for high wind conditions.
Mike Kintop, director of product management for Tremco Roofing & Building Maintenance, says that either concrete pavers or large aggregate provide the wind uplift and fire resistance for a ballasted roof. It’s typically only used with single ply roofing systems. “The ‘ballast’ means it’s a weight that is holding the roof down, and what provides the weight also functions to provide fire resistance,” Kintop says. The type of membrane doesn’t matter — it can be EPDM, PVC, or TPO under a ballast.
Stones In a Ballasted Roof
What’s holding that membrane in place is a field of rocks that are typically one and a half inch in size. For a ballasted roof with a higher wind uplift rating, the rocks might reach two and a half inches. Kintop says for a ballasted roof, a typical weight is 1,000 to 1,300 pounds per 100 square feet. This extra weight, of course, must be accounted for with a structural evaluation. He says that if there’s ballast on the building already, the building would most likely have been designed for it. This is why it is rare to see a building designed for a non-ballasted roof converted to a ballasted roof. Using pavers adds the weight in a similar way except without loose stones
.
Since the rocks or pavers are not adhered to the roof with any sort of adhesive, they’re just sitting on the roof, this system is only used on a roof with a slope of 12 or less. One type of ballasted roof is an IRMA (Inverted Roof Membrane Assembly), where the insulation is installed over the membrane rather than under it, and the ballast is then installed over the insulation with appropriate filtration layers and protection. Having the insulation above the waterproofing membrane will further protect the waterproofing membranes from weathering, physical damage, and fluctuation in temperatures since it’s under the insulation.
Kintop says ballasted systems are fairly inexpensive because of the low cost of the rock, which also provides a good fire barrier. These types of roofs can be installed in just about any kind of weather or temperature. “You can install a less expensive roofing membrane, theoretically, and it’s protected by the ballast that’s put on top, saving on labor, fasteners and adhesives,” he says. “You don’t have to mechanically touch the insulation, you don’t have to attach the membrane, you just loose lay the insulation and membrane and install the ballast over top.”
An IRMA Assembly
John Hamati, director of technical services for American Hydrotech Inc., says the term ballast often refers to stone as the ballast, but it’s not necessarily exclusive to stone. “A ballasted roof will have the membrane installed first onto the approved substrate, then followed by the XPS Styrofoam insulation and then the proper overburden,” Hamati says. XPS Styrofoam insulation is a closed cell polystyrene that is highly moisture resistant. Placing it on top of the roofing membrane offers protection from the harsh roof environment. American Hydrotech only uses XPS in their assembly as it can resist moisture.
This assembly of the membrane first and then the XPS Styrofoam is referred to as an IRMA, or PMR — Protected Membrane Roof. Keeping the insulation down can be accomplished in different ways depending on the desired finish . . . stone ballast, pavers on pedestals, wood tiles on pedestals, or even a green assembly like a garden roof. Concrete pavers or wood tiles utilize fixed or adjustable height pedestals for support. Those pedestals can compensate for slope and be adjusted to provide a leveled surface finish to the desired height.
“Anything that is above grade with occupied space underneath is considered a roof,” says Hamati. “A fifth-floor terrace over occupied space can be considered a roof. With a ballasted assembly, this roof can now become an amenity deck with hardscape, landscape areas and a pool if desired.”
Hamati says that one of the main advantages of going with an inverted roof assembly is the fact that it places the membrane on the structural deck. A conventional roofing arrangement can leave the membrane vulnerable to extreme and often sudden temperature changes, high summer roof temperatures, lower winter temperatures, freezing puddles, ultraviolet rays, physical abuse from foot traffic, and routine maintenance. Exposure to all these elements can weaken the integrity of the membrane. Once the membrane is compromised, moisture will eventually enter the insulation and cause a loss in its thermal efficiency. This will also lead to water migrating through the layers.
“Water can enter from the puncture and show up in a completely different location,” Hamati says. “However, when the waterproofing/roofing membrane is applied to the structural substrate, lateral water migration would be restricted.”
Uses Of Ballasted Roofing
Ballasted roofing can be used on anything, including plywood substrates, composite decks, gypsum board, and cement board. If XPS is used, the primary disadvantage is that XPS can not be left exposed. It has to be covered up and not left unprotected, even if the job is not completely finished. American Hydrotech has a product called Hydroguard, which is composed of Styrofoam panels topped with latex modified concrete which can be secured and kept in place either by using concrete pavers or a fabricated metal securement piece. This barrier protects the roofing membrane from temperature extremes and mechanical damage. It is useful for flat roofs where stone ballast is not practical.
With supply chain delays the industry is experiencing right now with roofing material and polyiso in general, many builders are discovering this roofing method. Hamati says the only place this assembly would not be recommended is if the building owner is looking to have insulation and a membrane as an exposed assembly. “Usually you would go to a traditional reverse,” Hamati says, “because you want a waterproofing membrane to hold the insulation down.”
Ballasted roofing is becoming more common, and this system is seeing usages even in areas that might not have typically been usable in the past. “By the building code, anything that is above grade with occupied space underneath can be considered a roof,” says Hamati. “A fifth-floor terrace can be considered a roof. With a pedestal and paver system, this can now become a barbecuing area and a building might also have a green landscape area with a pool. For those assemblies, you need an inverted roof assembly, so as those amenity decks are becoming more popular, this system is becoming more popular as well.”
Creating a roof deck of this type with a different type of roof causes problems because if there is a leak, most of the waterproofing membrane would have to be removed to chase down the damaged spot. “You can find it a lot easier,” says Hamati. “You’re protecting the waterproofing membrane, and since there might be things like plants growing on top, it’s easier to repair and chase a leak if there is one.”
However, if there is any damage, all of the ballast would have to be removed in order to do the repair.
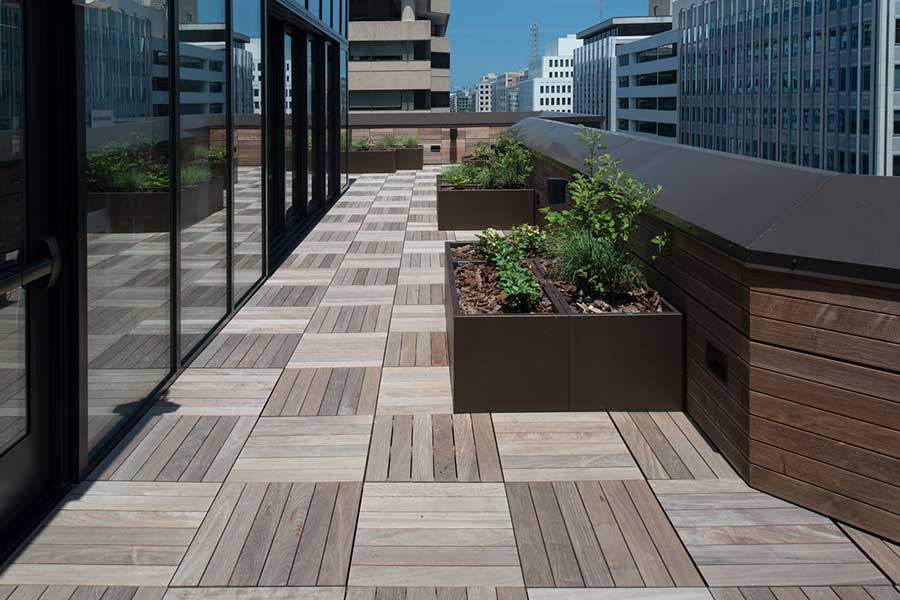
Ballasted roofing finished with wood tiles like this one allows roof areas to become usable areas such as terraces.
“You’ve got to move all of that ballast or overburden to try and locate the leak and then make your repairs and put the ballast/overburden back,” says Kintop. “If you have to go back in for more repairs, you’ve got to move the ballast again, which risks damaging the roof membrane along with the extra labor to move the rock.”
Conclusion
While ballasted roofing may not be as common as it was in the past, it seems to be making a comeback with a renewed focus on usable areas in commercial buildings and shared living areas such as apartments. Since the ballast protects the membrane from damage, doesn’t require any adhesives, and still has a high wind rating, it’s likely we’ll see more of these types of roofs in the future. Σ
Summer 2022 Back Issue
$4.95
Creating Livable Basements
Benefits of Ballasted Roofing
Why Your Waterproofing System Should Be Elastomeric
Choosing the Right Weather Barriers
AVAILABLE AS DIGITAL DOWNLOAD ONLY
Description
Description
Creating Livable Basements
By Vanessa Salvia
In homes that have a basement, an increasing number of homeowners are turning them into livable spaces like living rooms and bedrooms or offices. This makes the air quality even more important because people are using them for extended periods of time now.
Benefits of Ballasted Roofing
By Vanessa Salvia
A ballasted roof is a roof in which the roofing membrane is not anchored or adhered to the decking material but is instead held in palace by rocks or pavers. These roofs work even during high wind events, and they have other advantages too.
Why Your Waterproofing System Should Be Elastomeric
By Greg Austin
Waterproofing solutions for commercial construction projects come in a variety of materials or chemical make-ups. An elastomeric waterproofing material offers advantages due to its flexibility, durability, and high tensile strength.
Choosing the Right Weather Barriers
By Errol Bull, P.E., CSI
Whether it’s blazing heat and torrential downpour, or harsh winds and icy snowfall, buildings must withstand a range of extreme conditions, year after year. So, how do we make sure that our buildings are built to last?
Additional Info
Additional information
Magazine Format | Digital Download Magazine, Print Mailed Magazine |
---|