This space age structural repair material is moving beyond basements into above-grade commercial spaces, including the library at the University of Notre Dame.
Carbon fiber is truly a remarkable material. Its tensile strength is among the highest of any material known to man. And because carbon fiber will not stretch or break, even under incredibly high tension, it is rapidly gaining popularity for repairing below-grade structural concrete (See Working with Carbon Fiber in the Fall 2010 issue of this magazine).
But its use is not restricted to residential projects. This space-age structural repair material is moving beyond basement repair into parking garages, apartment buildings, even football stadiums.
Case Study: Below Grade
The Reinforcer, a carbon fiber reinforcement system designed primarily for residential basements, was recently used to reinforce a 370,000 sq. ft. retirement facility in suburban Philidephia.
The root cause was that—as construction on the multi-story project was nearing completion and many of the residents already moved in—building code inspectors uncovered a structural deficiency: Improper steel placement in the concrete below-grade walls. This made the facility’s 90,000 sq. ft. underground parking garage unusable. Even worse, the units above the garage were deemed uninhabitable, and the $21 million dollar project was at a standstill until the issue was resolved.
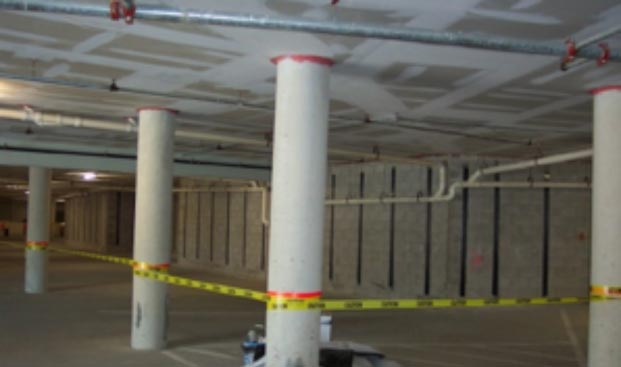
Carbon fiber strapping was used to reinforce a Pennsylvania parking garage, saving weeks of work and thousands of dollars in labor and materials.
Caldwell, Heckles and Egan, Inc., the general contractor, contacted John Ferguson, of Premier Building Restoration (Erdenheim, PA) to explore retrofit options.
Most of the 195 independent living senior apartments were already occupied at this time, and the underground garage was in constant use. This meant any repairs had to occur with the least amount of interruption to their daily activity.
Demolition and reconstruction of the garage’s walls would be disastrous to profitability. Steel I-Beams would inconvenience the residents. Ferguson’s firm had used carbon fiber strapping in residential work, and thought it might be feasible on this larger scale project. He reached out to Bob Thompson, owner of Nationwide Reinforcing Ltd. who also happens to be a Professional Civil Engineer.
Thompson and a team of independent structural engineers performed a detailed engineering analysis of the project, verifying lateral loads, the height of the walls and properties of the masonry and grout. They then identified the overstressed areas of the wall, and mapped them on engineering design charts. In the end, they concluded the carbon fiber Reinforcer was a cost-effective solution.
It’s essentially a 4” strap made of Carbon Fiber Reinforced Polymer (CFRP) measuring only .045” thick, about the same as a dime. The material is lightweight, non-corrosive and has a tensile strength of more than 350,000 pounds per square inch (psi), ten times stronger than steel.
Ferguson says, “The documentation and calculations Nationwide provided to the township engineer essentially proved that The Reinforcer would work and was the optimal solution for the application.”
It was cost effective, structurally sound, and met the tight time requirements. The remediation work went forward on a fast-tracked schedule.
Engineers determined the high-strength carbon strips needed to be placed on four foot centers for optimal spacing. Unlike steel beams, which only contact walls in the middle of the bow, the carbon fiber strips would be in continuous contact with the 11- to 15-foot tall walls.
Approximately 100, pre-cut, eight-foot-long Reinforcer® strips were applied with a structural epoxy paste along the interior surface of the foundation walls. Installers worked in sections to minimize any disruption.
Thompson notes, “Since The Reinforcer requires no digging, jack-hammering, moving utilities or duct work, the installation process takes approximately half the time of other methods.”
In fact, crews completed the installation in just two days.
Case Study: Above Grade
The University of Notre Dame is renowned for its football team, but also for the scholars it produces. And at the heart of that scholarship is the campus’ Theodore Hesburgh Library.
Built in 1963, the building’s façade features a massive mural of Christ with his arms outstretched. The mural is visible from the football stadium, and fans have given it the irreverent nickname “Touchdown Jesus.”
Exterior walls on the library are constructed from concrete block, laid up “stack bond” (i.e. in columns rather than with overlapping joints.) The building has a massive HVAC system, and over time, the air pressure created by the fans can create an almost imperceptibly small flexing. The weak lateral strength of the masonry pattern, combined with decades of small movement, eventually exceeded the strength of the mortar. By 2010, the cracks had become a major structural concern.
University administrators con-sidered the cost to replace and reconstruct the walls. However, the cost for replacement was significant due to the size and location of the walls. In the end, they chose carbon fiber to reinforce the walls and contain the cracks.
Rick Keller, P.E., owner of Keller Engineering designed a carbon fiber system that would create a a strong “shell” inside the air system and eliminate flexing. He specified The Stronghold from HJ3. Their certified installer, 3D Structural Solutions, performed the installation.
The library is the heart of campus, so to reduce any inconvenience of being shut down, installation was scheduled for Notre Dame’s winter break. The concrete was abraded with an abrasive blast, which removed any loose concrete. The cracks were injected with a compound that eliminates future movement. Then, the wall was primed and carbon fiber fabric strips were saturated and installed. For damaged mortar joints outside of the repair area, structural bonding cement was applied. Finally, the cured wall was covered with steel webbing to prevent any deflection with future pressure changes.
After the entire system was installed and the epoxy cured, they turned the HVAC system back on and ensured there was no deflection.
By using carbon fiber, the client saved several days and a significant amount of money compared to traditional steel beams. For superstitious Irish fans, they’re happy to know that Touchdown Jesus remains strong.
Spring 2013 Back Issue
$4.95
Properly Sizing Sump Pumps
Commercial Applications for Carbon Fiber:
Curtain Grouting in Residential Applications
PVC Membranes for Flat Roofs
AVAILABLE AS DIGITAL DOWNLOAD ONLY
Description
Description
Properly Sizing Sump Pumps
By Duane Friend
Sump pumps are the heart of most drainage systems, and they must be properly matched to soil conditions, pit size and other factors to eliminate short-cycling while still providing enough capacity for peak events.
Commercial Applications for Carbon Fiber:
This space-age structural repair material is moving beyond basement repair into parking garages, high rises, and other commercial spaces.
Curtain Grouting in Residential Applications
By Melissa Morton
Injecting polyurethane grout through below-grade walls to stop active water leaks is common in commercial work. But the technique has applications in the residential sector as well.
PVC Membranes for Flat Roofs
By Tony Matter
As the original single-ply roof membrane, PVC has a long and proven history. It’s still the roofing membrane of choice for many flat roof projects.
Additional Info
Additional information
Magazine Format | Digital Download Magazine, Print Mailed Magazine |
---|