Waterproofing manufacturers are constantly developing new and better products. New solvents and better water-based products provide better durability, improve protection, and keep the environment safer.
Many waterproofers continue to use tried-and-true waterproofing formulas invented decades ago. But new coatings can provide better protection, faster cure times, less health risk, and more durability than these older products ever can.
New, Safer Solvents
Nearly all spray- or roller-applied waterproofing materials consist of an asphalt or rubber polymer, held in suspension by a carrier liquid. Often, this carrier is a hydrocarbon, such as naptha or toluene. These chemicals, known as volatile organic compounds (VOCs), work extremely well. Unfortunately, some hydrocarbons can also be hazardous to the environment and the applicator’s health.
John Durkee, Ph.D., writing for Controlled Environments magazine, explains, “A generation ago, a table [of waterproofing solvents] would have contained only physical properties and chemical solvency. Since the 1980s, however, environmental, safety, and health considerations have become as—or more—important than chemical solvency.”
Solvents such as CFC-113 and trichloroethane were once common in waterproofing formulations because they were inexpensive, effective, versatile, and safe. Both are now banned—not because of health concerns, but because they damage the upper atmosphere.
Trichloroethylene, which was one of the most common asphalt solvents, was banned in 1996 as an ozone depleter by the Kyoto Protocol.
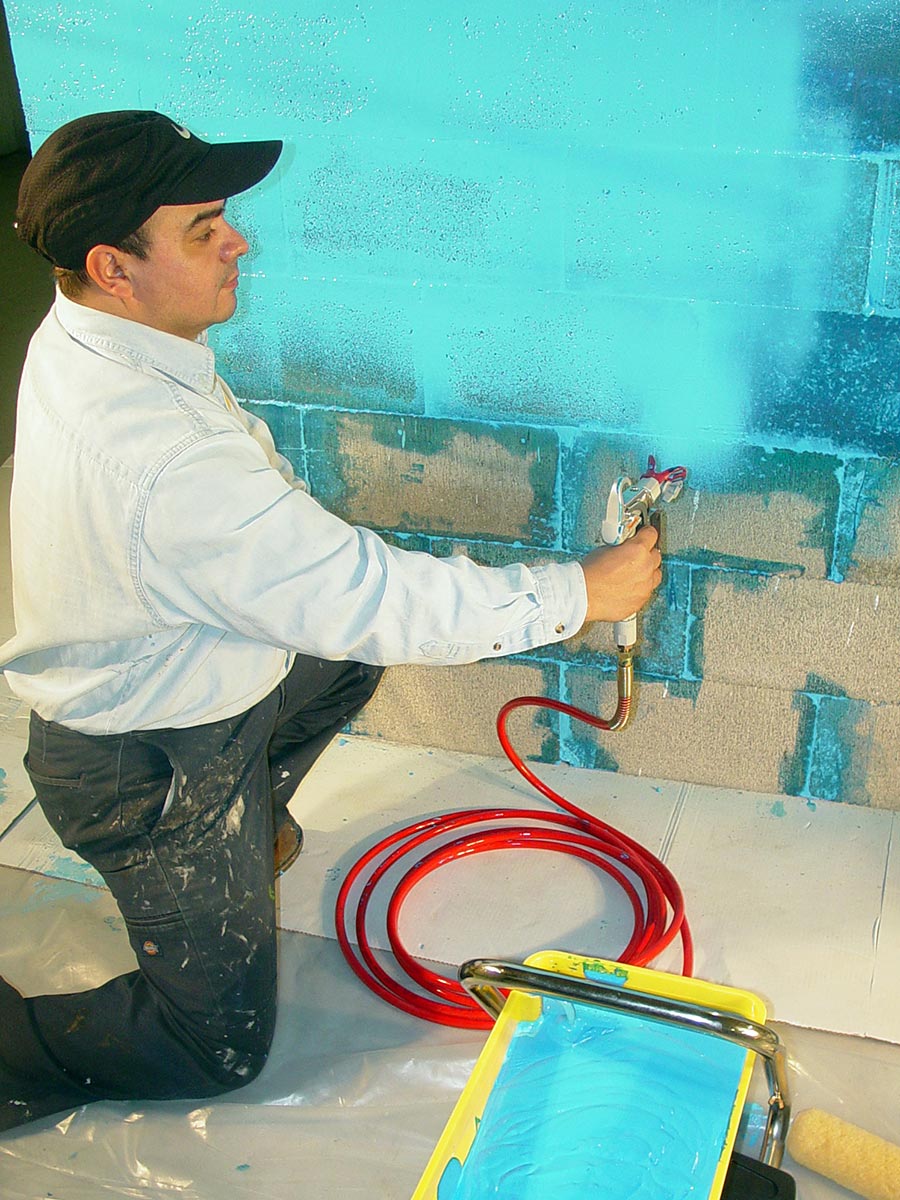
Most water-based coatings, like the Blue-Max from Ames pictured, can be applied to damp surfaces without risking delamination.
Chemists have been forced to develop so-called “designer solvents” to take their place. These are expensive, but the efforts have paid off. Products and processes which relied on the now-banned solvents are being replaced by
new ones. For instance, ASTM D2042 calls for the banned solvent trichloroethylene, but last month, the American Society for Testing and Materials (ASTM) approved a new standard, ASTM D7553, which uses the EPA-approved solvent n-propyl bromide instead.
“Since ASTM D7553 does not have a complete multi-laboratory precision statement, it cannot yet be substituted in the various specifications for buying and selling purposes,” said Stephen Burhans, a member of the committee that developed the new standard. “We will be working with ASTM’s inter-laboratory studies…to develop a complete precision statement later this year.”
Once those studies are complete, they will revise all the Roofing and Waterproofing sections that reference the now-obsolete ASTM D2042.
Water-Based Solutions
For contractors in the field, an easier solution may already exist. For just over a decade, a few manufacturers have produced water-based coatings that provide the same level of protection the solvent ones do. These have several advantages, including:
Non-toxic: While coveralls and a breathing mask are still recommended, water-based coatings have no bad smell, and there’s no need for special ventilation. Splashes or droplets that fall directly on the skin are not harmful, and can be cleaned off with soapy water.
Easy Clean-up: There’s no need for special cleaning agents for the equipment or the jobsite, either. Overspray and spills can be cleaned up with water, if it’s done immediately after application.
Versatility: Water-based coatings can be applied to substrates solvent based products cannot, including foam, plastics and bitumen. Additionally, they can be applied to both dry and damp surfaces. This is a major advantage in situations where the concrete hasn’t fully cured, rain has fallen, or wet soil has been removed to expose a foundation that needs to be treated.
That said, water-based products do have limitations. For instance, the product must be protected from freezing, and cannot be applied at low temperatures. Also, the coating must be allowed to cure fully before being exposed to rain, sprinklers, or other wetness.
Durability and Protection
Surprisingly, water-based products can provide unmatched durability and protection.
Peter Cary, sales and marketing manager for Ames Research Laboratory, explains. “The dinosaurs of the past have been cementatious, so they lack flexibility. Our products are rubber and allow elongation and minor cracking. Because they can flex and move with a structure as it settles and shifts, the durability of the waterproofing is greatly improved.
Ames’ Blue Max product is one of the most remarkable new coatings to come on the market in recent years. It adheres so tenaciously to concrete block that Cary has built demonstration water tanks more than 4 feet high using no mortar, just the Blue Max.
“This product has remarkable adhesion,” says Cary. “It flows into cracks and crevices as a liquid, and then sets up as a durable rubber to seal leaks wherever they occur. When it dries to impervious layer, it still stretches up to eight times its original length.”
Cary adds that it is an excellent choice for retrofit work. “It can be applied to a previously waterproofed surface with an asphalt emulsion or petroleum coating, without removing the old coating,” he states.
Epro Services makes Ecoline, a series of waterproofing products that offer exceptional durability. Like Blue Max, Ecoline is water-based, and offers excellent elongation and recovery to handle thermal movement as well as minor cracking. Ecoline also offers exceptional bonding. If applied properly, it will not delaminate from the substrate even with ponded water. Ecoline, available in the three different viscosities, builds up millage very quickly—almost instantly according to company literature—which allows application in inclement weather and eliminates shrinkage.
Another water-based product that offers many of these same attributes is Mel-Rol LM, a single-component, water-based, liquid waterproofing membrane from W.R. Meadows.
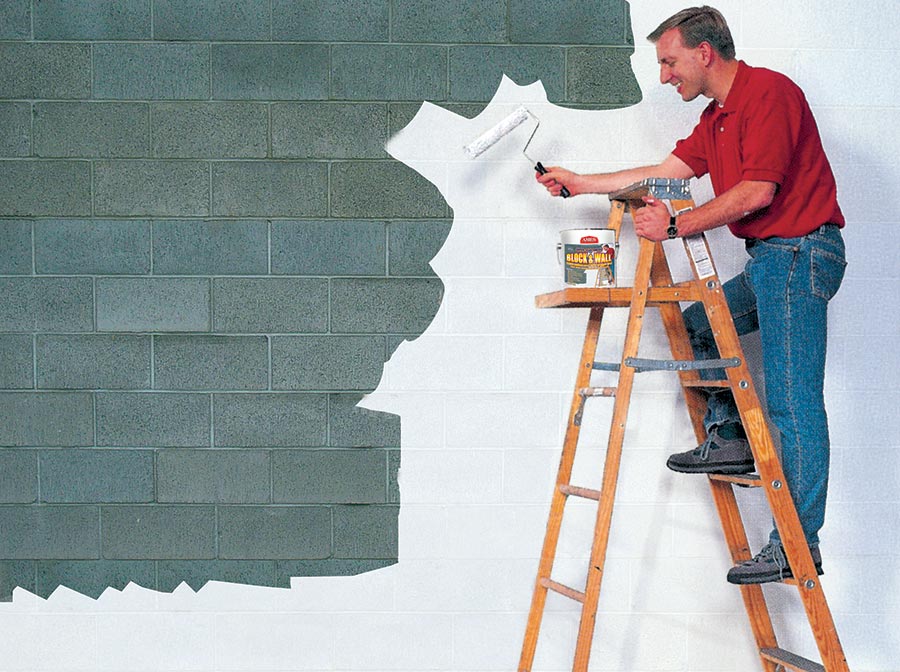
Many of these new coatings can be applied to small areas with a paint roller or concrete trowel.
Because the product is water-based and cold-applied, a variety of different protection courses, insulation boards or drainage boards can be imbedded into the membrane to create a superior waterproofing system. The product can also be applied over foam, such as on an Insulating Concrete Form (ICF) basement. With solvent-based systems, the foam could dissolve before the product cures.
One of the most flexible waterproofing products is Rub-R-Wall, made by Rubber Polymer Corp. In it’s fully cured state, it can stretch an astonishing 1800% without breaking or tearing. It is so durable that the company offers a lifetime warranty if applied on new foundations, and the company claims a product lifespan of more than 100 years.
The original Rub-R-Wall formulation is solvent-based, but the company now markets Rub-R-Wall Aqua, a water-based version rich in polymers that offers 1100% elongation and a tensile strength of 300 psi.
Savings
Any of these new water-based systems can be applied on damp or “green” concrete, as long as one side of the wall is exposed. This can create significant time savings—which often translates into improved profits for the waterproofer if schedules are tight.
But there’s another opportunity for profits as well. Because water-based products are cold-applied, the cost of the pumping equipment is much less. There’s no heater to buy, no “hard wired” hoses running between the truck engine and the pumping rig. The contractor can put the equipment on a trailer and drop it at the jobsite, with no need to leave an expensive truck at that location for the length of the job.
For small jobs, many products can be applied with a trowel or roller, eliminating the need for a pump altogether.
Finally, cure times for these new products are often faster. Ames Blue Max, for instance, is dry to the touch in about 2 hours usually, and can be backfilled soon after that. Ecoline has an initial cure time of only 10 minutes, and a final cure time of 24 to 48 hours.
The Future
Waterproofing manufacturers are constantly developing new and better products. If a contractor is spraying the same formulation he did 20 or 30 years ago, not only is he missing out on performance, but he’s missing out on the jobs he could be landing if he used more modern products.
In the last decade, several spray-applied membranes have hit the market that offer better durability, more protection, easier application, and higher profits. These attributes merit careful consideration.
Fall 2009 Back Issue
$4.95
Advances in Coatings
Green Decks and Planter Boxes
Below Grade Repair Strategies
Protecting a World Class Bridge
AVAILABLE AS A PDF DOWNLOAD ONLY
Description
Description
Advances in Coatings
The new generation of spray-applied waterproofing coatings provide better protection, faster cure times, less health risks, and more durability.
Green Decks and Planter Boxes
With construction similar to vegetative roofs, green decks and planter boxes preserve open space, reduce stormwater runoff, and protect the building envelope.
Below Grade Repair Strategies
This is one area of the business that does well regardless of the economy. Crack injection, piering, and carbon-fiber products all have their place.
Protecting a World Class Bridge
One of the world’s longest bridges. Stretching 5.6 kilometers (more than 2 .5 miles), is made almost entirely of concrete.
Additional Info
Additional information
Magazine Format | PDF Downloadable Magazine, Print Mailed Magazine |
---|