By Clark Ricks
Blindside waterproofing is one of the most difficult application methods. Here, Voltex, a bentonite sheet membrane from Cetco, had been applied to sheet pilings. The concrete wall will be poured after the waterproofing is in place, tied into the rebar visible at the bottom of the photo.
On most projects, below-grade waterproofing is applied after the foundation walls have been poured. On some projects, however, this is simply not possible. That’s where blindside waterproofing comes in.
With blindside waterproofing, the drainage and waterproofing membranes are installed before the concrete structure is poured. The concrete or other wall materials are put into place later.
“Blindside is a very difficult application to waterproof,” says Dave Polk, president of Epro Services. “You’re applying it over a soil retention system, not concrete or masonry. The problem is that you have to do your detailing against that retention system—whether that’s lagging beams, sheet pilings, or compacted native soils—instead of the concrete itself.”
Obviously, blindside waterproofing is considerably more complex than the regular way of doing things, but sometimes it’s the easiest—or only—way to get it done.
Blindside is often required on jobs where property lines and/or nearby structures limit excavation and access. Typical projects include “zero lot line” foundation walls, tunnels, and any jobsite in a high-density, build-up area.
Occasionally, designers may elect to use blindside waterproofing to limit excavation or to achieve “green” ratings. James A. Falconer at W.R. Grace explains: “Blindside waterproofing can substantially reduce the area of a site that needs to be disturbed or excavated to build and waterproof subterranean foundations,” he says. “It can minimize or eliminate over excavation and reduce the developed footprint of the building. Incorporating blindside waterproofing into a project design can help achieve LEED prerequisites or credits for Sustainable Sites-Site Development and other categories.”
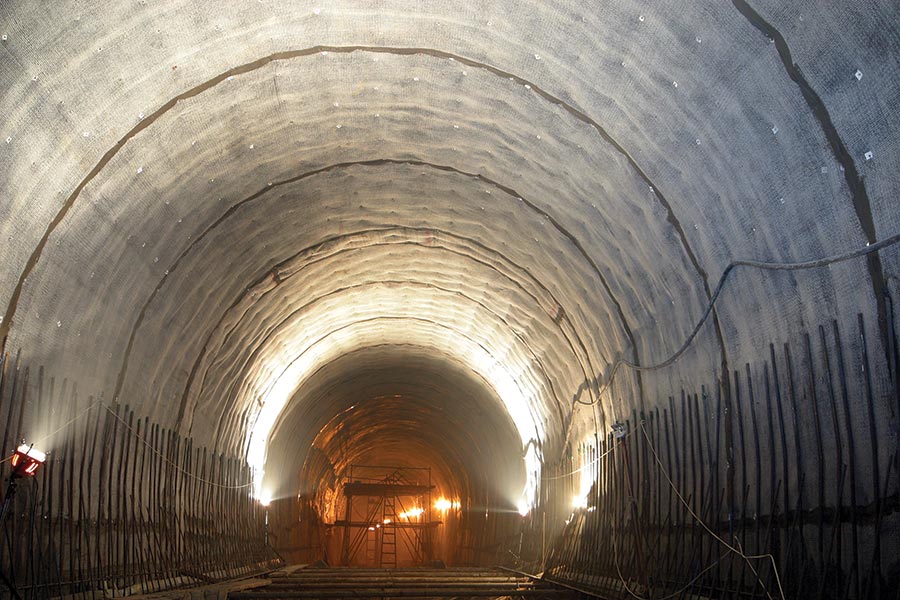
Tunnels are a classic example of why blindside waterproofing is necessary. On this job, contractors used shotcrete to stabilize the walls of the subway tunnel, then installed drainage sheets and Cetco’s Voltex bentonite for waterproofing. After the structural steel is placed, already completed in the lower portions of the tunnel, workers will place the concrete walls.
Despite the difficulties blindside presents, with the right materials and know-how, contractors can get good impermeable below-grade structures using blindside techniques.
Bob Walton, a general contractor and engineering geologist, gives this example. “I recently installed two new stair tower foundations for an existing three-story hotel building,” he writes.
The new foundations were deeper than those of the original building, which required underpinning the original structure so it wouldn’t settle into the vertical cut they dug alongside the building foundation.
“We then placed and secured sheets of bentonite [a natural clay that expands and seals when hydrated] up against the face of the cut. The bentonite in this case was attached to plastic drain sheets with filter fabric. In blindside basement waterproofing, everything is done in the reverse order of normal new foundation construction.
“The filter fabric side goes in direct contact with the soil of the vertical cut. The drain sheets came next, providing free drainage to relieve any hydrostatic pressure. The dry bentonite clay goes away from the vertical cut where it will be in direct contact with the freshly poured concrete. At the bottom, we ran perforated pipe and wrapped it in more filter fabric. After installing the reinforcing steel, we set forms to create the inside face of the new basement wall and then we poured the new concrete.”
Bentonite Sheets
Bentonite has historically been the solution of choice for blindside applications, and products like the one Walton used are made by numerous manufacturers. Bentonite is still popular in blindside waterproofing because it has the ability to heal itself if ripped punctured, or cracked; and once hydrated, the clay is virtually impermeable to water and most chemicals(i.e., acids, bases and hydrocarbons).
Carlisle Coatings & Waterproofing makes CCW MiraCLAY, a bentonite clay sheet encapulated between two sheets of geotextiles, needlepunched together with thousands of high strength denier yarns.
Cetco, the largest manufacturer of bentonite waterproofing products in the world, offers a number of bentonite products for blindside applications. In addition to Volclay Panels, the first bentonite-geotextile on the market, they also produce Voltex DS, which has a polyethylene liner added to the bentonite/geotextile product.
Cetco also markets Ultraseal SP, made from a bentonite-polymer alloy sandwiched between a durable polyethylene liner and a geotextile. The bentonite-polymer alloy is 100 times less permeamable than traditional bentonite and resists salts and organic contaminants better. The product has been successfully tested to 231 feet of hydrostatic pressure, and it weighs half as mush as some competing products.
Stacy Byrd, national products manager with Cetco, reports, “Bentonite/geotextile membranes are extremely durable and stand up to construction traffic and inclement weather. Bentonite/geotextile products are known for their performance and form a tenacious mechanical bond that locks them to the exterior surface of the concrete.”
Paraseal LG, made by Tremco Commercial Sealants & Waterproofing, is yet another option. It consists of a self-sealing, expandable layer of granular bentonite laminated at the rate of up to one pound per square foot to an impermeable, high density polyethylene (HDPE) sheet. Together, these two components form a tough, high performance membrane specially designed for blindside applications. Tremco notes that Paraseal LG can be exposed to the elements for relatively long periods of time, and is tough enough to withstand shotcrete applications directly on the face of the membrane.
Spray Applied Membranes
That was the problem designers of the Universal Studios Executive Office in San Francisco faced. The 50,000 sq. ft. underground parking structure sits four levels deep, so the waterproofing system had to be absolutely reliable. The lagging walls were held in place using a complex shoring system of tiebacks and rakers, so the waterproofing would have to seal around these irregular shapes. Additionally, the membrane would be exposed to the weather for months during construction. As a final challenge, it needed to be durable; the walls were to be constructed with shotcrete, which was to be applied directly to the membrane without a protection course.
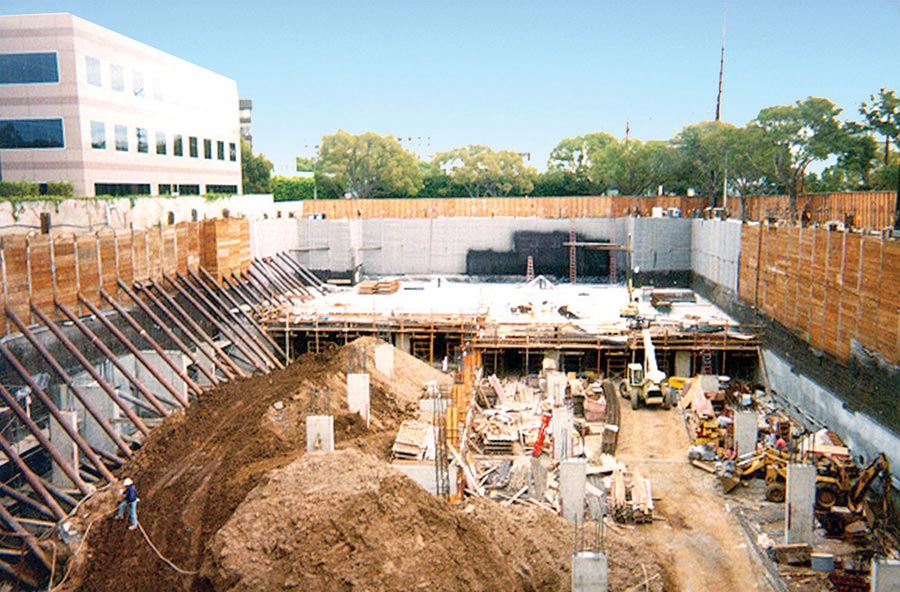
The Universal Studios project needed a membrane that could withstand 750,000 gallons a day of groundwater. It needed to be tough enough that the shotcrete could be applied directly on its face.
In the end, the design team chose Liquid Boot, by Cetco, a water-based polymer spray-applied membrane. The coating was sprayed to a uniform thickness of 100 mils. After it had cured, the shotcrete was applied directly to the membrane.
Now part of the finished structure, the waterproofing withstands an estimated 750,000 gallons per day of groundwater, directing it away from the building.
Epro Waterproofing Services also makes a spray-applied product for blindside applications. “We have a system that has numerous advantages over other products out there,” says Polk. The first step is fastening EcoDrain, a dimpled sheet drain, to the retaining wall. Then, the spray-on waterproofing membrane is applied. The Epro formula, called EcoLine, will chemically bond to the concrete wall when its poured.
“When the concrete cures, it creates heat and that bonds the product directly to the concrete,” says Polk. “The dimples in the drain mat also help ensure there will be no delamination between the membrane and the concrete. Really, the key to a good blindside application is the ability to detail around the soil retention system. Regardless of the system you use, the contractor must use some sort of liquid around the soldier beams, tie-backs, etc. What we offer is that the waterproofing membrane and detailing liquid is all the same seamless product.”
Epro was used to waterproof the commuter tunnel between I-88 and the San Jose International Airport. “Its basically a tunnel constructed in the middle of a water table,” says Polk, “and because of the water table, you couldn’t use lagging.”
Soil engineers compacted bentonite and cement into the soil to create temporary tunnel walls. “That’s what we waterproofed against,” he says. “The water table was six feet below grade, and we were 25 feet below that.” His company waterproofed the 180,000 sq. ft. of tunnel walls without a single leak. “Two nearby tunnels used different approaches, and they leak all the time.”
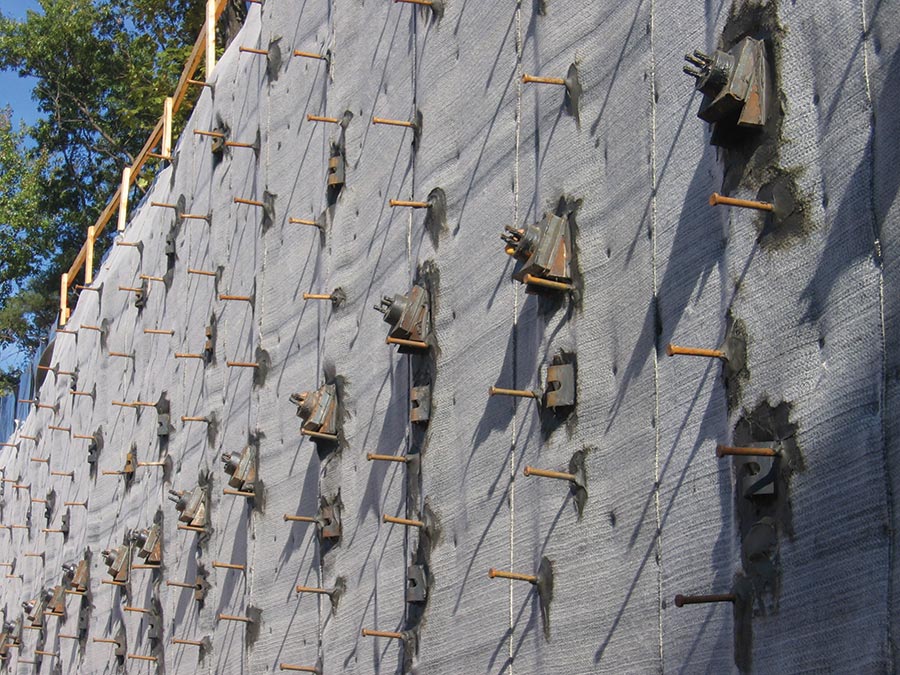
Because earth retaining systems can be complex, the level of detailing required on blindside jobs is extreme. “Really, the key to a good blindside application is the ability to detail around the soil retention system,” says Dave Polk. “Regardless of the system you use, the contractor must use some sort of liquid around the soldier beams, tie-backs, and other penetrations.”
Plastic Sheet Goods
Some blindside projects use plastic sheet goods, which use a variety of methods to ensure good adhesion between the concrete and the membrane.
Enkadri Pour & Proof by Colbond, for instance, will permanently embed itself into the concrete. The sheet is about ¼ inch thick and has two layers: a 60 mil reinforced bitumen waterproofing membrane, bonded to a mesh of tangled nylon fibers which will embed themselves into the concrete as the wall is poured. Depending on the application, a separate drainage mat may need to be installed between the lagging wall and the waterproofing membrane.
Underseal Blindside from Polyguard is another option. First, a drainage layer is fastened to the wall, and any penetrations are sealed with a liquid waterproofing compound. Finally the 73 mil Underseal product is applied. It’s actually a 4 mil thick sheet of HDPE laminated to a 56 mil layer of proprietary waterproofing compound bonded to a 13 mil nonwoven geotextile fabric.
In a reaction similar to Epro, when the concrete is poured, the heat creates a mechanical bond to permanently secure the concrete to the membrane.
A final choice is Preprufe 160R from W.R. Grace. It consists of a HDPE film coated with an aggressive pressure-sensitive adhesive and a weather resistant protective coating. The pressure-sensitive adhesive forms a continuous mechanical bond to concrete that is cast against it, eliminating the possibility that water could work between the membrane and structure.
Blindside waterproofing is becoming increasingly common. Bigger structures are being built on less desirable land. Jobsites are becoming more congested and the nascent green-building movement is encouraging owners to keep excavation to a minimum.
There’s a host of products designed to make the complex process as simple as possible. Bentonite clays have a proven track record stretching back half a century or more. Spray-on products and sheet goods are more recent, but most have been used at jobsites around the country for decades.
Regardless of the product you choose to specify or install, working closely with the manufacturer and others on the construction team will go a long way to guarantee that the structure performs as intended for decades to come.
Fall 2007 Back Issue
$4.95
This is the Very first issue of WATERPROOF! Magazine.
Blindside Waterproofing
Project Profile: Roofing a Historical Landmark
Footing and Drainage Boards
AVAILABLE AS A PDF DOWNLOAD ONLY
Description
Description
This is the Very first issue of WATERPROOF! Magazine.
Blindside Waterproofing
Occasionally, waterproofing and drainage membranes have to be applied before the below-grade structural wall is built. Here are the products and techniques the experts use.
Project Profile: Roofing a Historical Landmark
The 140-year-old Salt Lake Tabernacle needed a new roof. The challenge was that it is one of the most complex—and famous—roofs in the country. Having the congested jobsite right in the middle of Utah’s most visited tourist attraction added another degree of complexity.
Footing and Drainage Boards
The key to ensuring a good, waterproof basement depends as much on the drainage system as the waterproofing membrane itself. Drainage boards relieve hydrostatic pressure by directing water to the base of the structure. Footing drains remove that water away from the building.
Additional Info
Additional information
Magazine Format | PDF Downloadable Magazine, Print Mailed Magazine |
---|