By Vanessa Salvia
Foundation drains, also called footing drains, are typically installed adjacent to the footing on the outside and/or inside of the building structure to help prevent water damage.
Water seepage into a building’s foundation is one of the biggest threats to structural integrity. Moisture or water can enlarge cracks and create leaks and encourage mold growth and poor air quality — all of which can damage the entire structure or cause it to be uncomfortable and unlivable.
Foundation drains, also called footing drains, are typically installed on new construction to help prevent water damage. Foundation drains are attached to the foundation on the outside of the foundation wall. They prevent water from reaching the foundation and also route water away from the foundation toward a drain.
What Is A Drainage Board?
A drainage board can be single- or multi-layered and often made of polypropylene. Some of them are covered with an engineered textile. Drainage boards go on top of the spray-applied system or peel-and-stick waterproofing system. The dimpled plastic sheets come in various lengths. The dimpled side is placed toward the foundation and the dimples create a slight air gap between the sheet and the wall. The plastic creates a barrier, and the dimples move any water that does collect either through condensation or a leak, away from the wall and toward a foundation drain. The types that are covered with textile fabric have the fabric attached to the dimpled side. The fabric allows the water to pass to the dimple core and reduce the hydrostatic pressure in the ground, while also trapping any dirt or debris that may be in the water.
What Is A Foundation Drain?
Foundation drains, also called footing drains, are typically installed adjacent to the footing on the outside and/or inside of the building structure to help prevent water damage. These footing drains are typically made out of corrugated pipe with thousands of small holes that let water in. The pipes are usually covered with a fabric that lets water pass through but not dirt or debris. The drains should be installed around the entire structure. When used as a system with dimple foundation boards, the boards drain water toward the foundation drains and the foundation drains convey water away from the structure to daylight or toward a storm system or sump pump. Without drainage boards and foundation drains, water can pool around the foundations of a building.
Vincent Boccia, of Boccia Bros. Waterproofing and Masonry Specialists in New York, is a licensed professional engineer with a master’s degree in groundwater hydrology. Boccia Bros. is a third-generation waterproofing company that has been installing drainage systems since the 1950s. Boccia prefers using footing drains with fabric because the fabric eliminates the potential of clogging and allows them to offer a longer guarantee. Pipe systems are typically corrugated polyethylene made with open slits to allow water into the pipe; polyethylene tubing is the preferred material as it is flexible and installed with fewer fittings. Boccia recommends a minimum of 4-inch diameter piping. “When you factor in all the costs involved in preparing the channel and laying the tubing, it’s pennies on the dollar to go to the 4-inch drain and the 4-inch is the minimum size that should be installed,” he says.
When the foundation drain is installed on the inside adjacent to the footing, it will serve to dewater the soil immediately below the floor. Boccia says that in decades past builders would leave a quarter-inch channel between the inside foundation wall and the basement floor. “In 1986, we invented the Hollow Kick Molding, which is specifically designed to allow the passage of water through this channel,” he says. “But the whole point is to have a channel.” Boccia says there is a common misconception about the channel. He says people often think that the channel is designed to allow water that comes down inside of a wall to get to the drainage system. “But the real reason for that channel is to allow air to escape,” he says. “It’s the same reason why you punch a hole in both sides when you open up a can. In order for that water to flow properly in the drainage system, air must be allowed to escape. The secondary purpose is that if any water comes down the foundation wall, it will go into the system.”
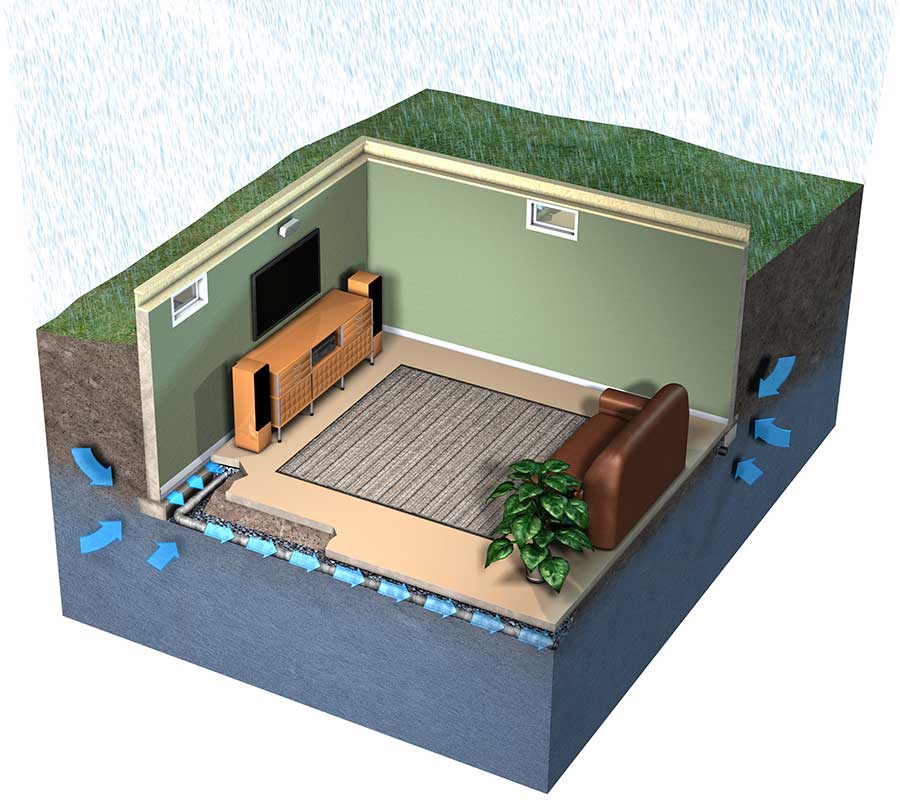
When a basement has proper drainage, water enters the wall but is moved away and does not enter the livable area.
Applying Exterior Drainage Boards to ICF Structures
Cory Deyell, the North American sales representative for DMX Membranes, says there can be some waterproofing and drainage challenges with ICF foundations. For one, foam blocks can be affected if backfilling is not done carefully. “The smooth finish on polypropylene snap ties can allow water to wick inside the foam block and concrete and seep through the foundation into the living space,” he says. He also notes that ICF blocks themselves have seams between every block which gives water direct access to the concrete if waterproofing is not applied correctly.
“Standard concrete foundations traditionally have steel snap ties every 16 to 24 inches,” says Deyell. “Depending on the ICF manufacturer, ICF blocks can have up to four times as many separators, which increases the chance of water getting to the concrete and finding its way into the living space.”
Drainage boards can help protect the weak points of a foundation by reducing hydrostatic pressure in the ground, which gets rid of standing water and takes the pressure away from possible structural issues. “DMX Drain 5X was designed as a residential/light commercial drainage board,” says Deyell. “It not only provides great drainage, but it also acts as a protection board against backfill and stone slinging.” The HDPE material it is made from resists stress cracking and also resists alkalis and acids found in the soil, which can damage materials over time. As with other drainage boards, the negative side (flat side) of the drainage board lays against the ICF foundation. “This prevents cutting of the foam blocks and protects them from site conditions,” says Deyell. “The heat-bonded Spun-Bond Polypropylene fabric faces towards the backfill to create an air gap/drainage channel between the drainage board and the soil. The filter fabric prevents soil and other impediments from clogging the drainage channel while allowing water to release from the soil and pass through the fabric which then drains to your foundation drainage system. This reduces the hydrostatic pressure in the ground.”
Deyell says he always recommends that customers with ICF foundations use a drainage board as opposed to a standard foundation wrap. “A foundation wrap is designed to have an air gap between the foundation and the membrane itself,” Deyell says. “This allows condensation to build between the membrane and the foundation wall. A drainage board prevents water from getting behind the membrane and into the ICF foundation.”
Spring 2023 Back Issue
$4.95 – $5.95
Crack Repair For Foundations
Waterproofing in High Humidity
Drainage Boards and Footing Drains
Residential Basement Waterproofing
Case Study 1: The Hyatt House Miami
Case Study 2: Bowed Block Wall Repair
Case Study 3: Miami’s Brickell View Terrace Apartments
Description
Description
Crack Repair For Foundations
By Vanessa Salvia
Different repair methods are used based on whether
the cracks affect the structural integrity or not.
Waterproofing in High Humidity
By Vanessa Salvia
High humidity does affect some aspects of waterproofing, and here’s what you have to keep in mind.
Drainage Boards and Footing Drains
By Vanessa Salvia
Water seepage into a building’s foundation is one of the biggest threats to structural integrity.
Residential Basement Waterproofing
By Holly Richards-Purpura
Addressing a nasty crawl space and a damp, leaking basement before selling a home.
Case Study 1: The Hyatt House Miami
The Hyatt House Miami Airport Hotel in South Miami, Florida, required more than 30,000 square feet of Polystick XFR roof underlayment.
Case Study 2: Bowed Block Wall Repair
A contractor from EcoSpect used Rhino Carbon Fiber’s Bowed Wall Repair Kits to reinforce a CMU basement wall.
Case Study 3:
Miami’s Brickell View Terrace Apartments
M3 Roofing complete a 6,000-square-foot re-roof project using a self-adhered, multi-ply roofing system from Polyglass.
Additional Info
Additional information
Weight | N/A |
---|---|
Magazine Format | Digital Download Magazine, Print Mailed Magazine |