By Steven H. Miller
New Digitally-Fabricated Aquarium Tank Liner Can Stand the Test of the Giant Tuna
In 2011, the Monterey Bay Aquarium in Monterey, California replaced the tank-liner in its million-gallon open sea exhibit.
The 80-foot-long tank is shaped like an eggshell. It’s built of ¼”-thick Fiber Reinforced Polymer panels (a composite similar to fiberglass) supported by a series of massive FRP ribs. It is the “scenic backdrop” of the tank, designed to create the effect of looking into the featureless depths of the sea.
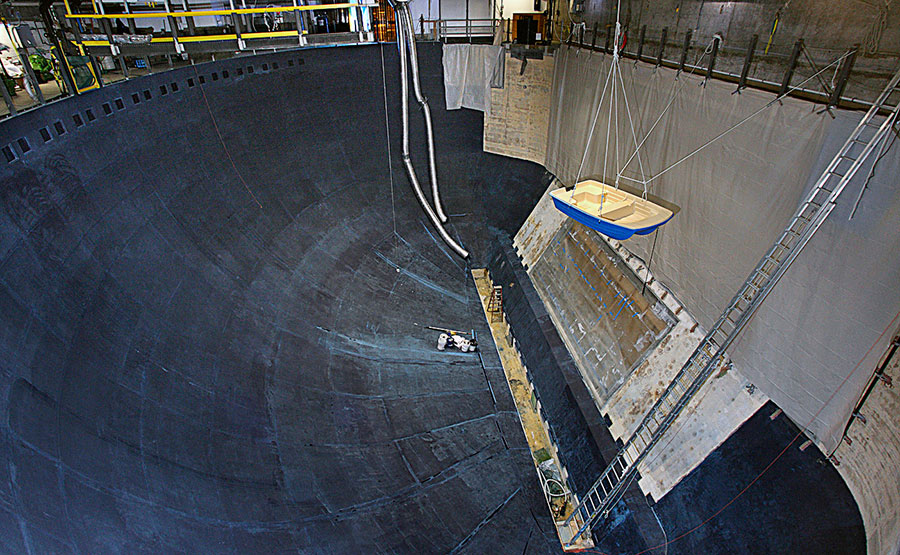
The Monterey Bay Aquarium recently replaced the vast liner of its million gallon tank with a ¼-inch thick, deep blue shell made of fiber reinforced polymer (FRP).
The original liner, installed when the exhibit opened in 1996, had suffered damage due to unforeseen animal behaviors. The large fish swimming at high speed during feeding created enough turbulence that the liner flexed slightly. Over time, this loosened the grout that held the thousands of small blue glass tiles onto the liner surface. Combined with occasional impacts from large, fast-swimming tunas, many tiles became dislodged and created an unsightly surface.
The aquarium needed a new liner, and understandably insisted on minimal downtime. They hired Kreysler & Associates (K&A), a consulting firm with experience using composite materials in structures. They recommended fabricating the entire liner off-site, draining the tank only when the liner was ready to install.
The new liner’s design is a significant improvement over the original, based on knowledge acquired from the first 16 years of the exhibit. Instead of using tile, it uses a special gelcoat to achieve a deep blue color. Unlike the colored gelcoats available in the mid-1990s, the new cutting-edge material is hard and abrasion-resistant, and maintains a rich clarity of color, even when continuously immersed in saltwater for years. The new gelcoat was tested by the California Department of Fish and Game and the University of California, Davis to ensure it was nontoxic to marine life.
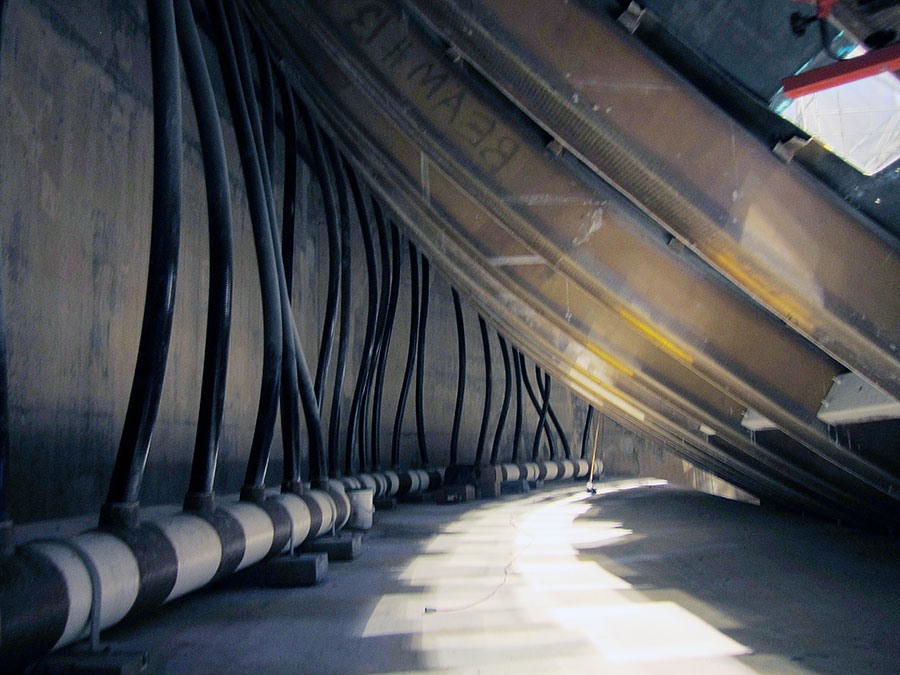
The large support ribs of the liner, seen here from the rear side, are also made of FRP. The original ribs were able to be reused for the new liner, even after 15 years in the water.
Another challenge was to give the ¼”-thick liner enough strength and impact-resistance to absorb the blow from a 250-lb tuna traveling at 25 knots. The FRP material was up to the task. “This is a highly versatile material,” observes Bill Kreysler, president of K&A, “not only in terms of appearance, but also as a structural component. Once the tuna problem was identified and the impact forces were known, we could design for it.”
However, K&A had to design and fabricate the liner without direct measurements, since the “jobsite” was still occupied by a million gallons of seawater and dozens of large fish. The plan called for re-using the original support structure, but K&A did not have direct access to its exact dimensions and curvature. The original, documented dimensions of the support ribs could not be relied upon either, because 16 years under heavy load would have predictably caused them to sag and reshape.
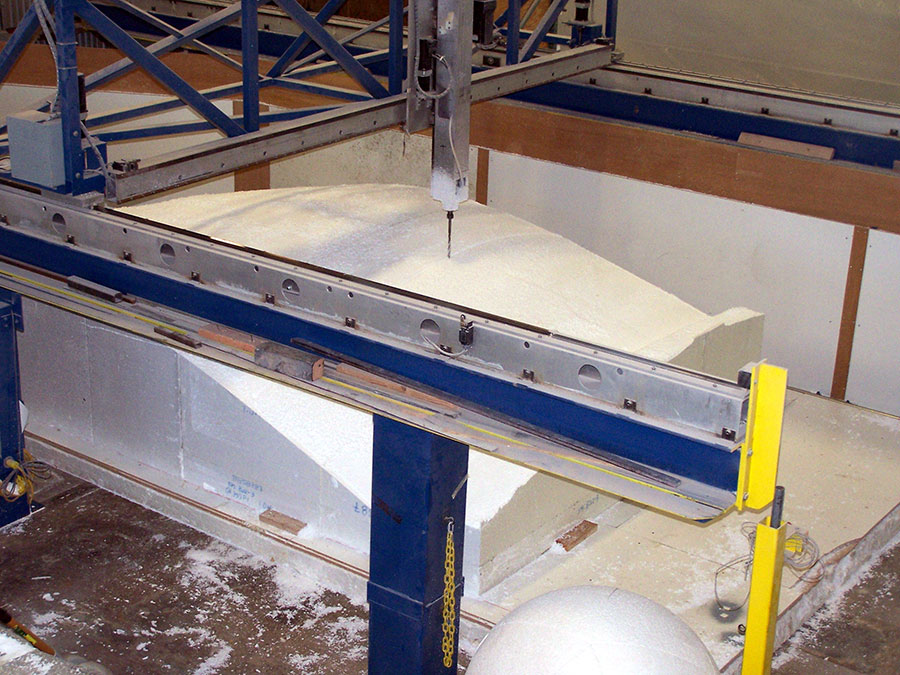
The computer-designed curves of each section of liner were accurately carved onto expanded polystyrene (EPS) foam blocks by this large, gantry-mounted Computer Numerically Controlled (CNC) router. The EPS foam served as a mold to build up the multi-layered FRP composite shell.
Under these conditions, measurement of the existing structure was limited to educated guesses that could be made from the top surface of the tank. Using that sketchy information as a starting point, K&A created a 3-D computer model of the curved surface, roughly an eggshell with part of its top and front side sliced off.
The liner was to be assembled onsite from 180 pre-molded sections, each with unique curvatures measuring approximately 10×12 feet. The panels were shaped on molds made from large blocks of expanded polystyrene (EPS) foam. The EPS foam was shaped by a gantry-mounted CNC milling machine that nibbled down the EPS to precise curves.
To allow for differences between their estimates and the actual structure, K&A allowed generous overlaps on each panel, trimming them to size at the jobsite.
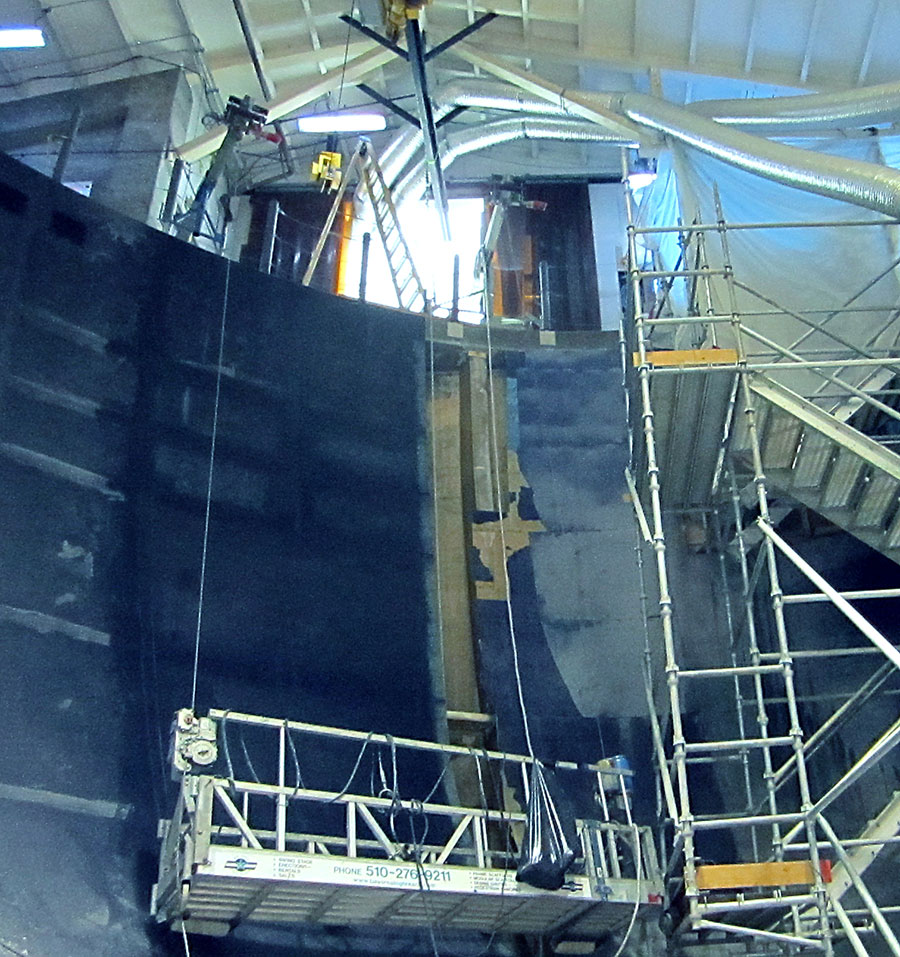
Swing-stage scaffolding was used to install the new FRP panels on the existing rib structure.
It took three months to fabricate the panels. Then they were transported to the site, the tank was emptied, and the animals sent to board elsewhere. Installation was complicated, as the bottom of the tank was curved and wouldn’t support scaffolding. Instead most of the panels were installed using a hanging platform suspended from the top edge of the tank. During the final finish work, installers worked from a floating platform that rose as the tank was filled. After four months of installation, the liner was completed. Following weeks of refilling and reconditioning the water, the animals were slowly introduced back into the exhibit.
“This is one of the major attractions of the Monterey Bay Aquarium,” explains Marty Manson, the aquarium’s project director. “It exhibits animals from the open ocean. The concept is that you’re looking into their habitat: the deep blue depth, open water.” It is the environment for some of the largest, most charismatic, animals in the aquarium.”
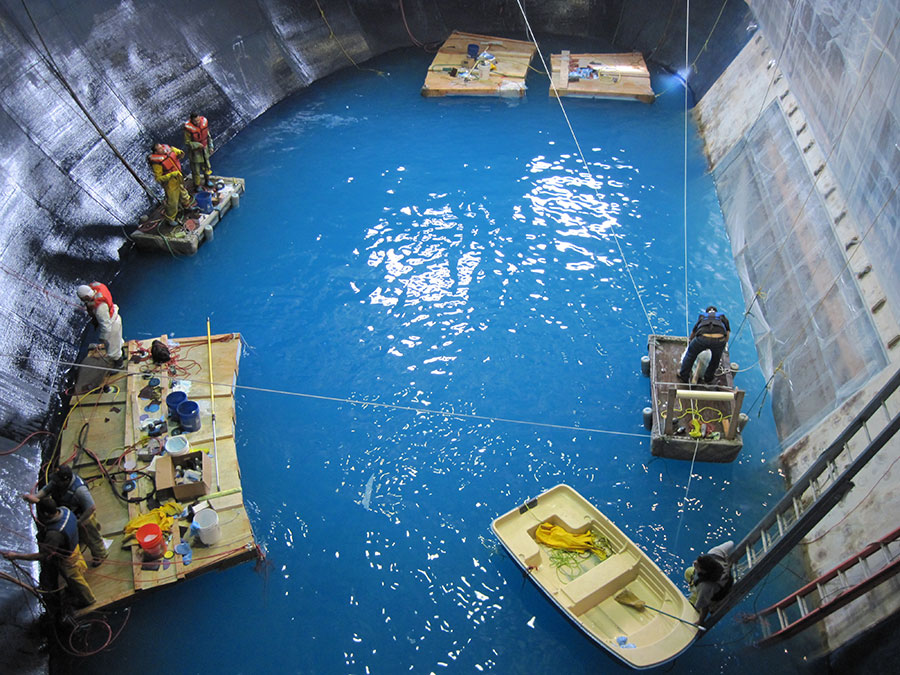
Installers used floating platforms to do final finishing on the ¼” thick shell. The color effect of the liner, when seen through water, is quite striking. The plastic sheeting on the right covers the main viewing window of the tank.
“Like many of our projects, this was one-of-a-kind,” he continues. “Technology, engineering and new materials all made it possible. What made it happen was a lot of very hard work by a smart and dedicated fabrication/installation crew and on-site team. We expect it to last a long, long time.”
Fall 2013 Back Issue
$4.95
Electronic Leak Detection: High Vs. Low Voltage
Basement Finishing Kits
Blindside And Underslab Work
Project Profile: Monterey Bay Aquarium
AVAILABLE AS DIGITAL DOWNLOAD ONLY
Description
Description
Electronic Leak Detection: High Vs. Low Voltage
The need to quickly find and repair leaks in roofing membranes has never been higher. Two new electronic leak detection methods are rapidly gaining popularity because they can locate even the smallest leaks with pinpoint accuracy.
Basement Finishing Kits
By Ron Greenbaum
It’s now easier than ever to offer basement finishing services. A number of companies offer innovative prefinished “kits” that make this a profitable service for many waterproofing contractors.
Blindside And Underslab Work
Projects that require waterproofing to be installed before the structural concrete require reliable, durable products, and flawless workmanship.
Project Profile: Monterey Bay Aquarium
By Steven H. Miller
Rebuilding and sealing a million-gallon aquarium tank was challenging—especially with a tight timetable and a requirement for non-toxic materials.
Additional Info
Additional information
Magazine Format | Digital Download Magazine, Print Mailed Magazine |
---|