By Gregory Fahrenbruch
Photos courtesy of Gregory Fahrenbruch
Asbestos-containing tiles in a basement where a home had water damage.
Employers responsible for asbestos-related issues differ from those who do not work with asbestos but may have a potential for exposure to those who work abating asbestos products. There are also responsibilities to building managers, general contractors, and multi-employer workplaces.
Employees Who May Be Exposed To Asbestos
OSHA has a “General Duty Clause,” from the OSHA Act of 1970, which requires that, in addition to compliance with hazard-specific standards, all employers provide a work environment “free from recognized hazards that are causing or are likely to cause death or serious physical harm.” Employers in the waterproofing business who do not work with asbestos have a duty to ensure the materials they disturb are free from asbestos materials. This is done through asbestos surveys conducted by an accredited inspector. The inspector will take the proper number of samples for the materials that are slated for disturbance and have them analyzed by an accredited laboratory. If all the samples come back negative for asbestos, then you can proceed.
OSHA mandates that employees with potential exposure go through annual asbestos awareness training. In an awareness class, the employees are taught the health hazards of asbestos and generalities of what is “potential asbestos-containing materials” (PACM) in their business. A good course will have pictures and/or samples of materials that employees may run across. How disturbances occur also needs to be covered. The training needs to be recorded with the attending employee’s name, date of training, and topics covered. The company needs a written asbestos policy. Each employee should sign that they have read and understand the company’s position with the discovery of PACM during any course of the project.
Employees Who Have Exposure To Asbestos
Employees who have exposure to asbestos must have initial medical exposure assessments as mandated by OSHA, OSHA-mandated respirator questionnaires, a medical evaluation with pulmonary function tests (PFT), and lung X-rays. Medical evaluations must be renewed annually. The medical information is to be kept for 30 years and be on each jobsite. A written respiratory protection program, training documentation, and respirator fit testing must be kept on the jobsite. A daily roster of each employee who works on the jobsite during the asbestos removal process must also be kept. During the project, the employer is responsible for conducting an initial exposure assessment and an 8-hour time-weighted average of asbestos exposure. The initial exposure assessment dictates the type of respiratory protection that will be required during the duration of the day’s activities. At REST, we use Powered Air Purifying Respirators (PAPR) for the duration of each project because they give us 1,000 times more protection than a negative pressure respirator and they lessen the breathing stress over a negative pressure respirator. The downside of a PAPR is that the battery packs need to be charged at the end of each day, they are prone to damage within the motor and wiring, and their cost starts at around $600. Repairs to PAPRs can commonly go up to $450 for a new motor, depending on how the parts are sourced.
Each employee who is working in an abatement company needs to complete an initial abatement training. This can be in the form of a worker card or supervisor card. When on the jobsite, each employee must have their card on hand and the employer needs to have a copy of each employee’s card along with the employee’s annual training certificate that was obtained by an accredited trainer for the state they are working in. The card and the training must both be up to date. It is important to realize that an abatement worker could have a fully approved accreditation card, but if their training is out of date, that means they cannot be on the jobsite in an active abatement role. That’s right! Many states do not have reciprocity for asbestos training qualifications and accreditation cards.
So, if you met all the training, medical, and carding requirements, you still need to have an approved asbestos license for the company. This means the lead person in the company needs to submit at least their training documentation they used to obtain their current accreditation card, their current accreditation card, workers compensation policy, hazard communication policy, respiratory protection policy, and pay a fee to obtain an annual abatement license.
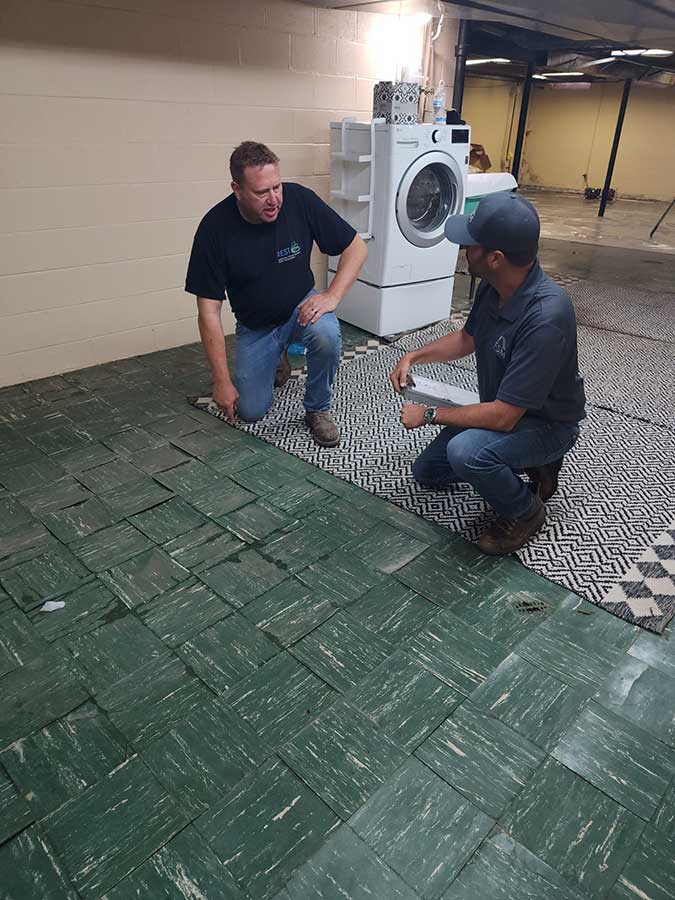
The author, Gregory Fahrenbruch, explains to Andrew, of Foundation Systems of Michigan, that these asbestos-containing tiles need to be removed. The homeowners were going to install a french drain and a sump, but the company cannot send their employees in to do the work because the tile will crumble, causing a safety issue. The basement had chronic water damage, and these tiles were heavily damaged.
Responsibilities of General Contractors
General contractors have overall responsibility for their jobsites. No matter how a contract may be written between a general contractor and an abatement contractor, the general contractor still holds legal supervisor responsibility over its abatement contractor. The law sees the general contractor and abatement contractor as both equally responsible for worker protection. This means if an abatement contractor (as a sub) is fined for not following regulated work, let’s say $4,000, then the general contractor also has the same exposure. Now, consider the size of your company. The fines are scaled based on the size and history of each company, so the abatement contractor may get a $4,000 fine but the GC may get a fine for the same items because of their general authority of $12,000 based on their size and history. The general contractor is also responsible for holding all documentation related to the job they subcontracted out related to employees for 30 years.
General contractors also must share information related to ongoing asbestos projects with other trades on a site. This can cause major issues among trade groups. I suggest that a general contractor schedule abatement projects when only abatement will be done without any other trades onsite. It’s not uncommon that the abatement project will become the main topic of discussion at jobsite, in a negative way, whether the project goes off without a hitch or not. The fact that an asbestos abatement project is being conducted can instill fear among all the trades.
Other Situations
If a company is an LLC, the owner of the LLC is considered to be an employee of the company. In that regard, the owner of a company is considered to be an employee and must follow the same rules and regulations that other employees do.
Also, the only person who can have asbestos removed from a home is the person who actually has their name on the title. For instance, if Grandma owns a house with an asbestos problem and the son is working on the house on her behalf, the son is not authorized to have the asbestos removed. If Grandma compensates the son in any way, then he could be considered an employee of Grandma’s, which makes him have to follow the same regulations that other employees follow.
The Bottom Line
Employees who have a potential for exposure to asbestos need to be annually trained on how to recognize PACM. A written asbestos policy is required, and sign offs are required. Before disturbing any PACM, it needs to be evaluated by an accredited asbestos inspector. Abatement contractors must annually train their staff, have medical evaluations completed, and ensure that employees hold up-to-date accreditation cards for the state they work in. All documentation must be up-to-date offsite. Having an employee qualified to remove asbestos does not mean the employer can remove asbestos, because they need to be properly licensed to do so. General contractors who subcontract asbestos work hold the same legal responsibilities as their subcontractors.
Greg Fahrenbruch
Greg Fahrenbruch founded Restoration Environmental Safety Technologies, or REST, in Ortonville, Michigan, in 2010. He is an industrial hygienist with a degree from Ferris State University with expertise in asbestos removal. He holds state accreditations as an asbestos inspector, asbestos contractor supervisor, management planner, and asbestos-licensed contractor. He also has a background in insurance restoration. Contact him at greg@restenvironmental.com.
Fall 2023 Back Issue
$4.95 – $5.95
AI in the Waterproofing Industry
Case Study: Northwestern University’s Simpson Querrey Biomedical Research Center
Installing and Protecting Green Roofs
Protecting the Commercial Building Envelope
Understanding Hydrostatic Pressure
Employer Responsibilities To Employees and Law
By Gregory Fahrenbruch
Description
Description
AI in the Waterproofing Industry
By Vanessa Salvia
It may be something you have to get used to, but once you do, it could be extremely useful and valuable.
Case Study: Northwestern University’s Simpson Querrey Biomedical Research Center
By American Hydrotech
The building’s proximity to Lake Michigan creates a high water table issue for the building.
Installing and Protecting Green Roofs
By Vanessa Salvia
There are many benefits of green roofs. However, successfully installing and maintaining a green roof requires careful planning and protection to ensure the plants thrive.
Protecting the Commercial Building Envelope
By Vanessa Salvia
Envelope performance directly impacts occupant comfort, health, energy efficiency, durability, and operating costs.
Understanding Hydrostatic Pressure
By Vanessa Salvia
When water accumulates and cannot drain properly, hydrostatic pressure builds up and pushes against the waterproofing membrane or material.
Employer Responsibilities To Employees and Law
By Gregory Fahrenbruch
Employers responsible for asbestos-related issues differ from those who do not work with asbestos but may have a potential for exposure to those who work abating asbestos products.
Additional Info
Additional information
Weight | N/A |
---|---|
Magazine Format | Digital Download Magazine, Print Mailed Magazine |